INTERGRANULAR CORROSION
The third type of corrosion, intergranular, is not
visible on the surface and is very dangerous. It spreads
through the interior of the metal along the grain bounda-
ries, reducing the strength and destroying the ability of
the metal to be formed or shaped. Among the metals
affected by this type of corrosion are stainless steel,
certain magnesium alloys, and the copper-bearing alu-
minum alloys.
Intergranular corrosion occurs in certain grades of
stainless steel when the steel is heated as in welding.
Brittleness results, and later the metal cracks near the
weld. For this reason, a post-weld heat treatment is
needed before you reinstall stainless steel parts that
have been welded.
As an ABF, you are going to be concerned mainly
with the first two types of corrosion, surface and
galvanic. With this in mind, remember that rust on
steel and the white powder on aluminum or magne-
sium are produced by corrosion. These products,
along with dirt and salt, pick up moisture from the air
and hold it in contact with the metal, which speeds up
the corrosive action.
CORROSION REPAIR
There are many factors that affect the type, speed,
cause, and seriousness of metal corrosion. Some of
these corrosion factors can be controlled; others cannot.
Preventive maintenance factors, such as inspection,
cleaning, painting, and preservation, are within the con-
trol of the operating activity.
When you first find corrosion on equipment or a
structure, the first step you take should be the safe and
complete removal of the corrosion deposits or replace-
ment of the affected part. Whether you remove the
corrosion or replace the part depends upon the degree
of corrosion, the extent of damage, the capability to
repair or replace, and the availability of replacement
parts. Any parts that have been damaged by corrosion
should be replaced if continued use is likely to result in
structural failure. Areas to be treated to eliminate cor-
rosion deposits must be clean, unpainted, and free from
oil and grease. Chips, burrs, flakes of residue, and
surface oxides must be removed. However, be careful
to avoid removing too much of the uncorroded surface
metal. Corrosion deposit removal must be complete.
Failure to clean away surface debris permits the corro-
sion process to continue even after the affected areas
have been refinished.
When corrosion is present, any protective paint
films must first be removed to ensure that the entire
corroded area is visible. After you remove corrosion,
the extent of damage must be assessed. It is at this
point that you determine whether to repair or replace
the affected part or to perform a corrosion correction
treatment. The correction treatment involves neutral-
izing any residual corrosion materials that may re-
main in pits and crevices, and restoring permanent
protective coatings and paint finishes.
CORROSION PREVENTION
Corrosion can be controlled by maintaining a dry
environment using suitable moisture barriers or drying
agents. CLEAN, DRY METALS DO NOT COR-
RODE. Therefore, when moisture and dirt are perma-
nently removed from metal surfaces, the tendency of
such surfaces to corrode is usually eliminated. Thus, it
follows that the major problem in the prevention of
corrosion consists of adequately removing moisture and
dirt from the surface of the metal to be protected and
covering these surfaces to prevent recontamination.
Consistent preventive maintenance is the most
practical method of controlling metal corrosion. Main-
tenance such as cleaning, painting, and preservation
shows great savings in labor and materials by eliminat-
ing costly repairs and replacements required when cor-
rosion has been permitted to go unarrested.
To effectively remove oil, grease, dirt, and other
undesirable foreign deposits, you should use certain
cleaning agents, such as soaps, solvents, emulsion
compounds, and chemicals. When you work with
these agents, you should follow the correct method
and sequence of procedure in applying them. You also
must follow the accepted safety regulations and health
precautions in the use and handling of the various
cleaning agents. The important factors bearing on the
choice of cleaning materials are the type and surfaces
to be cleaned, such as painted or unpainted surfaces,
and whether they are exterior or interior parts.
Uses of Paint
To prevent corrosion of metal (or deterioration of
wood surfaces), you should repaint damaged or worn
surfaces as soon as practical. Repaint no more often than
is necessary for preservation. In the Navy, paint is used
primarily for the preservation of surfaces. It seals the
pores of wood and steel, arrests decay, and helps prevent
the formation of rust. Paint also serves a variety of other
purposes. It is valuable as an aid to cleanliness and
sanitation, both because of its antiseptic properties and
because it provides a smooth, washable surface. Paint
also is used to reflector to absorb light or to redistribute
2-33
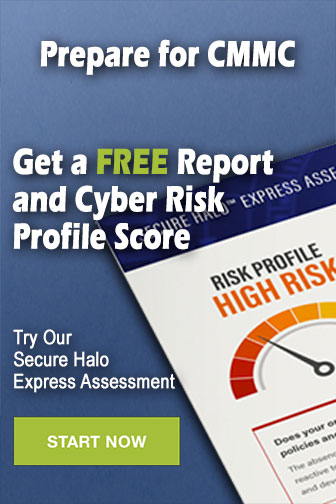