The chemical air drier removes excessive moisture
from the bleed air. Dry, clean air is sent to the
reservoir through the check valve, air regulator, and
relief valve.
TWO bleeder valves are installed in the flight and
combined system reservoirs. One is found on the air
side of the reservoir and the other on the fluid side.
The air side valve permits the bleeding of air pressure
during system maintenance. It allows the bleeding of
any hydraulic fluid seepage past seals to the air side.
The fluid side bleeder reduces excessive fluid level
and bleeds air from the fluid side.
Quick-disconnect fittings in the hydraulic power
systems permit easy pump or engine removal without
loss of fluid to the system. The fittings connect
ground hydraulic test stands for maintenance
purposes. The pump disconnects should not be forced
together against the back pressure of a pressurized
reservoir or system. Forcing disconnects together
may result in damaged seals in the male ends of the
disconnects. When the disconnects do not slide in
smoothly, they should be removed and checked for
proper seating of the O-rings. Replace seals if they
are damaged. The seal goes on top of the O-ring.
When the disconnects are uncoupled, the ends not
being used should be properly protected from dirt and
other contamination.
Use only approved metal
closures.
EMERGENCY POWER SYSTEMS
According to the military specifications, which
establish the requirements for aircraft hydraulic
systems, all hydraulically operated systems
considered essential to flight safety or landing must
have provisions for emergency actuation. The
specifications further state that these emergency
systems may use hydraulic fluid, compressed gas,
directed mechanical linkage, or gravity for their
actuation.
Some aircraft use mechanical linkage or gravity
in conjunction with pneumatic pressure for
emergency actuation of landing gear and other
actuating systems where limited actuation is required.
Most other essential hydraulically operated systems
have emergency power systems that are powered by a
hand pump, electric motor-driven pump, ram-air
turbine-driven pump, or a pneumatic compressor.
On some aircraft the hand pump is a part of the
auxiliary hydraulic system and is not considered as
part of the emergency power systems. The hand
pump is used for ground operation of the canopy,
extensible electronics platform, nose radome opening,
and to recharge the brake accumulator. These
systems may be operated by aircraft system pressure
or, if the aircraft is shutdown, they may be powered
by the auxiliary electric motor-driven hydraulic pump
or the hand pump.
HYDRAULIC COMPONENTS
Learning Objective:
Identify the various
hydraulic system components and recognize
t h e p r o c e d u r e s r e q u i r e d f o r t h e ir
maintenance.
Various types of hydraulic components makeup a
power system. The components discussed in this
chapter are representative of those with which you
will most likely be working. Values such as pressure,
temperature, and instructional tolerances have been
given to provide detail in the coverage.
When actually performing the maintenance
procedures discussed, the exact location and make up
of the various hydraulic and pneumatic components
will vary with the design of the hydraulic system.
You should consult the current applicable technical
publication for the latest information on items such as
location, pressure, temperature, and tolerances.
RESERVOIRS
The reservoir is a tank in which an adequate
supply of fluid for the system is stored. Fluid flows
from the reservoir to the pump, where it is forced
through the system and eventually returned to the
reservoir.
The reservoir not only supplies the operating
needs of the system, but it also replenishes fluid lost
through leakage. Furthermore, the reservoir serves as
an overflow basin for excess fluid forced out of the
system by thermal expansion (the increase of fluid
volume caused by temperature changes), the
accumulators, and by piston and rod displacement.
The reservoir also furnishes a place for the fluid to
purge itself of air bubbles that may enter the system.
Foreign matter picked up in the system may also be
separated from the fluid in the reservoir, or as it flows
through line filters.
7-5
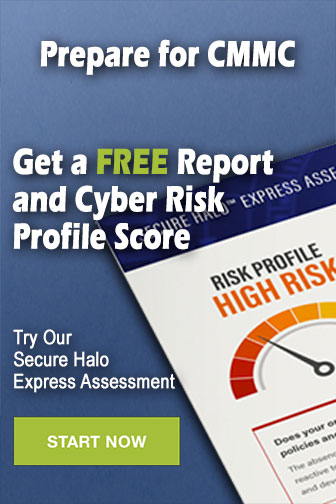