inch in diameter, attached directly to the tank
drain outlet, or trailer fill-drain outlet, is
recommended by current directives. All flare
fittings must be perfectwithout dents, scratches,
or toolmarks. Do not use any antiseize compound
on threads or any cleaning compounds on sampler
parts. Contamination will result. A sampler
received without residual pressure probably leaks.
Such samplers should be rejected and returned.
Just before sampling, remove the cap from the
sampler valve; open the valve to release shipping
gas pressure, then reclose. Next, remove the valve
by disconnecting the adapter from the nipple, and
place the cylinder upright in a holder.
Attach the separator and line assembly to the
tank drain or fill-drain outlet. Using a trailer
pressure of 10 to 20 psi, let the LOX flow into
an open container, such as the receiving vessel
shown in figure 5-10, for at least 30 seconds to
purge the line. Adjust the pressure to obtain a
quiet, uniform, full flow from the separator outlet
tube.
Wipe the frost from the separator outlet tube,
and immediately insert the outlet into the sampler
tube and fill it. The filling will take approximately
1 minute. When liquid splashes in droplets over
the top, the tube assembly is full. The sampling
tube holds about 180 milliliters (6. 12 oz) of LOX,
which produces a maximum pressure of 300 psi
when vaporized in the closed sampler.
NOTE: During the filling operation, the
operator should wear a face shield, hat, gloves,
and other protective equipment as excessive
pressure will violently throw LOX from the tube
assembly.
As soon as the sampler tube is filled, remove
the separator from the sampler assembly and
install the adapter to the cylinder. Close it tightly
with end wrenches, making sure that the valve is
fully closed. Turn sampler upside down for a few
minutes to allow liquid to flow from the sampler
tube into the cylinder. Immerse the valve of the
cylinder in water to check for leaks.
PURGING
Purging and other maintenance of LOX
trailers is performed by the AS rating.
Purging is the cleansing of impurities from
oxygen systems and containers. There are two
ways to purge oxygen containers, LOX wash and
gas purging.
5-14
The LOX wash method is used on large
containers, such as storage tanks and LOX
trailers, to lower the contamination to acceptable
levels by replacing the contaminated LOX with
LOX known to be uncontaminated.
To do this, drain the container using the
buildup coil. Do NOT open the vent during this
operation. Partially fill the container with un-
contaminated LOX and allow the container to
stabilize. Build up pressure to 30 to 40 psi and
then vent the pressure to 0 psi. Repeat this opera-
tion for a total of three cycles. Take a sample and
forward it to a designated site for analysis. If the
sample is acceptable, the container may be put
into service. If the sample is not acceptable, the
container must be gas purged using hot water
pumped nitrogen.
If allowed to run dry or if odor is detected in
the system, aircraft LOX converters must be gas
purged before being put into service. Gas purg-
ing of aircraft LOX systems must be done if any
maintenance is performed on the system that
opens it to the atmosphere.
To gas purge a LOX converter, first drain the
converter of LOX. If possible, allow the converter
to warm to ambient temperature. This saves vast
amounts of nitrogen. Attach a purging device to
Figure 5-11.Purging unit ready for use.
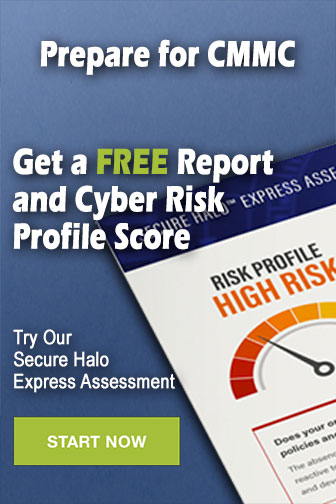