number (PN), national item identification number
(NIIN), nomenclature, avionics system name, avionics
system number, and line item number. The line item
number cross-reference is optional, provided only
when specifically requested by the user. The
cross-references provide a rapid means of identifying
and locating the position of an item in the body section.
They are the key to proper use of the IMRL. An
example of a part number cross-reference listing is
shown in figure 3-10.
IMRL main body. This section lists all items
allowed for the activity, and shows the authorized
allowance quantity for each item allowed. Each
subsection of the IMRL lists applicable nonavionic,
government furnished, aircraft equipment (GFAE)
following the last line item number listed in that
subsection. Each page in the IMRL main body (fig.
3-11) presents identification data, description data,
and land vessel (LV) code, maintenance level data,
accountability data, and allowance data. Depending on
the type of activity to which the IMRL applies, the
main body may be have one or more subsections (or
support categories of equipment).
Each subsection (or support category) may have
two parts, depending on single model application or
multimodel applications. Part I contains items that
apply to a specific model in an activitys IMRL. Part
II contains items that apply to more than one model in
an activitys IMRL. The facility subsection contains
only part II and defines all applicable work centers.
The page heading format for the IMRL main body
(fig. 3-11) is presented both vertically and
horizontally. The IMRL legend lists page headings.
Each IMRL main body page starts with preparation
date, report title, file name, page number, subsection,
model, AAI, activity name, and activity reportable
code. For multiple applications, multi appears as the
model.
The column headings identify the type of
information contained in each column. These headings
and the data element contents of each column are
defined in NAVAIRINST 13650.1.
IMRL Activity Inventory Record. This record lists
all items that are on inventory at the applicable activity
on the date this section is prepared. It is reissued in its
entirety each month. It provides identification data,
management data, inventory status, authorized
allowances, and nomenclature for each item (fig.
3-12).
Current procedures provide for IMRL tailoring,
since SERMIS source data does not necessarily reflect
peculiarities such as geographic factors or certain
operating conditions. Upon receipt of a new IMRL,
each activity will review the allowances for accuracy
and adequacy for its support requirements. A primary
function of tailoring is to eliminate or reduce common
or general-type SE quantities by supporting a mix of
weapons systems or components. Tailoring also serves
to uncover errors in the IMRL that affect not only the
particular aircraft mix supported, but also may affect
the support of aircraft and systems at other similar
activities. The two methods of tailoring an IMRL are
IMRL activity tailoring and the SECA tailoring
conference.
IMRL activity tailoring. All maintenance
activities are responsible for submitting IMRL revision
requests (fig. 3-13) as a post-review of tailoring actions.
Maintenance activities submit IMRL revision requests
following the procedures outlined in NAVAIRINST
13650.1.
SECA tailoring conference. The SECA
representative makes on-line tailoring actions as a result
of a SECA-held tailoring conference.
Q19.
What are the major sections of the IMRL?
Q20.
What section of the IMRL lists all of the items
allowed for the activity along with allowance
quantities?
Q21.
How often is the IMRL Activity Inventory Record
reissued?
MATERIAL REQUIREMENTS
LEARNING OBJECTIVE: Define the purpose
of the Material Control work centers and the
jobs performed by the personnel assigned.
Whenever a need arises to do a job, the tools,
supplies, and equipment that are needed generate
material requirements. The supply department fills
these requirements.
The material control center (MCC) at the
organizational and intermediate levels (O and I levels)
of maintenance is the point of contact for material
needed by maintenance personnel.
3-17
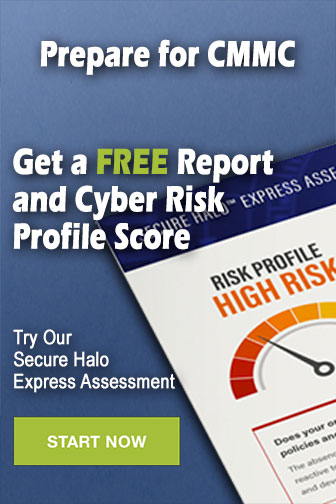