in the figure, by the activity that initiates the record.
Subsequent entries are made by activities that maintain
custody of the equipment.
The operating interval is the authorized time
between overhauls for the particular equipment. The
data required for the replacement interval is obtained
by review of the Replacement Interval Data block on
each Assembly Service Record (ASR), Module Service
Record (MSR), and Scheduled Removal Component
(SRC) card. The lowest time recorded is written as the
replacement interval on the AESR. The replacement
due is computed by adding the lowest interval time to
the engine time. Entries are made in pencil to allow for
component changes at repair or rework activities.
The block titled Current Engine or Propeller
Position No. is used to indicate the engine or propeller
position number (1, 2, 3, or 4) as installed on the
aircraft. This position indicator aids in the placement
of associated accessory and other supplemental records
in the correct equipment record.
Equipment Operating Record (OPNAV
4790/31A)
The Equipment Operating Record (fig. 8-2) is
intended for use with all aeronautical equipment that
requires the monthly compilation of significant
operating data and is unique to the AESR. Reporting
custodians ensure that operating or monitoring system
data is entered on this form at a monthly interval and
upon transfer of the equipment.
The Equipment Operating Record provides
columns for the logging of operating hours or
monitoring system data, as applicable. Operating hours
are obtained from record type (RECTYP) 7B of the
Naval Aircraft Flight Record. Uncaptioned columns
are provided for monitoring system data and are labeled
as required; for example, starts, rounds fired, low cycle
fatigue (LCF), and meter reading. If equipment is
monitored by time since new (TSN) or time since
overhaul (TSO), the first column under monitoring
system data is labeled TSN or TSO, as appropriate. The
cumulative column under operating hours will then
show TSN or TSO hours. The Remarks column is for
the logging of additional information, as appropriate.
Q5. What type of data is recorded on the Equipment
Operating Record?
Q6. Entries should be made on the Equipment Operat-
ing Record at least monthly. On what other
occasion should an entry be made on this record?
Inspection Record (OPNAV 4790/22A)
The Inspection Record, shown in figure 8-3, is one
of the forms that is common to both the aircraft logbook
and AESR. The maintenance of the form is the same
for the aircraft logbook and AESR. The heading blocks
on each form are filled in to identify the type of
inspection and the equipment name, model, and serial
number.
A major engine inspection, phase inspection,
special inspection, and conditional inspection (except
fluid sampling, engine wash, or servicing) all require an
AESR entry by the activity that performs the
inspection.
Phase and major engine inspections are logged on
the same Inspection Record page.
Special and conditional inspections are logged on
separate Inspection Record pages as follows:
Equipment that has an AESR and requires a
nondestructive inspection (NDI) or disassembly and
reassembly is logged on an Inspection Record page
titled SPECIAL.
A conditional inspection is an unscheduled
inspection required as a result of an overlimit condition
or as a result of a circumstance or event that creates an
administrative requirement for an inspection, such as a
hot start or overtemp. A conditional inspection is
logged on an Inspection Record page titled
CONDITIONAL.
Acceptance and transfer inspections on uninstalled
equipment are NOT logged on Inspection Records.
During first-degree repair, the intermediate
maintenance activity (IMA) screens the Inspection
Record and, during rework, the depot-level
maintenance activity screens the Inspection Record.
The old Inspection Record pages for scheduled
maintenance are removed, and a new record that
contains the data necessary for determining when the
next scheduled inspection is due is initiated.
Conditional Inspection pages are screened for items of
historical or maintenance value and transcribed to a
new page. A minimum of 2 years of data is maintained
at all times on the Conditional Inspection page.
8-3
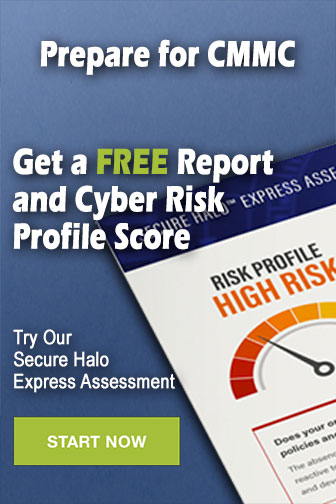