Figure 15-32.Forehand welding.
Figure 15-33.Backhand welding.
welding rod back and forth in opposite semicircular
paths, you balance the heat to melt the end of the rod and
the side walls of the joint into a uniformly distributed
molten puddle. As the flame passes the rod, it melts off
a short length of the rod and adds it to the puddle. The
motion of the torch distributes the molten metal evenly
to both edges of the joint and to the molten puddle. This
method is used in welding most of the lighter tubing and
sheet metals up to 1/8 inch thick because it permits better
control of a small puddle and results in a smoother weld.
The forehand technique is not the best method for
welding heavy metals.
BACKHAND WELDING.In this method the
torch tip precedes the rod in the direction of welding,
and the flame is pointed back at the molten puddle and
the completed weld. The end of the rod is placed
between the torch tip and the molten puddle. The
welding tip should make an angle of about 45° to 60°
with the plates or joint being welded (fig. 15-33).
Less motion is required in
than in the forehand method.
the backhand method
If you use a straight
Figure 15-34.Four basic welding positions.
welding rod, it should be rotated so that the end will roll
from side to side and melt off evenly. You may also bend
the rod and, when welding, move the rod and torch back
and forth at a rapid rate. If you are making a large weld,
you should move the rod so as to make complete circles
in the molten puddle. The torch is moved back and forth
across the weld while it is advanced slowly and
uniformly in the direction of the weld. Youll find the
backhand method best for welding material more than
1/8 inch thick. You can use a narrower V at the joint
than is possible in forehand welding. An included angle
of 60° is a sufficient angle of bevel to get a good joint.
It doesnt take as much welding rod or puddling for the
backhand method as it does for the forehand method.
By using the backhand technique on heavier
material, it is possible to obtain increased welding
speeds, better control of the larger puddle, and more
complete fusion at the root of the weld. Further, by using
a reducing flame with the backhand technique, a smaller
amount of base metal is melted while welding a joint.
Backhand welding is seldom used on sheet metal
because the increased heat generated in this method is
likely to cause overheating and burning. When welding
steel with a backhand technique and a reducing flame,
the absorption of carbon by a thin surface layer of metal
reduces the melting point of the steel. This speeds up the
welding operation.
WELDING POSITIONS.The four basic welding
positions are shown in figure 15-34. Also shown are four
15-25
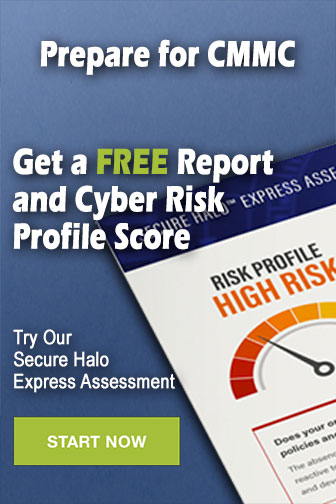