multiple locations, record the total quantities in all
locations on the count document. Personnel who do the
counting must ensure that the quantity and unit of issue
of each item inventoried are compatible. For example,
if the total count of an item is 100 and the unit of issue
is pair (PR), the inventory count should be 50 PR.
Inventory personnel should record or check the actual
location(s) of material in the count documents. If the
prerecorded location does not contain the item, enter a
0 (zero) for quantity inventoried. In some cases,
inventory personnel may find the item in another
location. If it is impractical to put the item in the
prerecorded location, delete the prerecorded location
and add the new location. Enter the new location and the
quantity in the inventory documents. Inventory
personnel are also responsible for keeping themselves
apprised of all pending transactions in the inventory
segment. These are the receipts, issues, or other
transaction documents of items included in the
inventory. Inventory personnel should stamp or mark
these transaction documents with BEFORE
INVENTORY or AFTER INVENTORY, as
appropriate.
REVIEWING THE COUNT DOCUMENTS
Inventory personnel must review the count
documents to ensure that all items scheduled for
inventory are counted. During the review, they should
ensure that quantities are legible and have a correct unit
of issue, and that all added items are identified and
legibly recorded. Enter any remarks legibly and state
them explicitly. When using manual inventory
procedures, document each item in NIIN sequence.
Inventory personnel should ensure that count
documents have the date and initial of the person who
counted the items.
RECONCILING COUNT DOCUMENTS
AND STOCK RECORDS
Physical inventory procedures include comparing
the inventoried quantities with the quantities in stock
records to check if there are differences. If the inventory
and stock record quantities match, post the inventory
and date of inventory in the stock records. Also, enter
the inventoried quantity in the stock record to reflect the
on-hand balance.
If differences exist, stock control personnel should
reconcile the records. Reconciliation is the process of
resolving inventory discrepancies. Reconciliation
process consists of several steps. It is dependent upon
the type of material, cost, and the circumstances that led
to a discrepancy. The reconciliation process may include
conducting a preliminary or a causative research. It also
includes processing inventory adjustments or
adjustment reversals and maintaining supporting
documentations.
A major difference exists when the physical count
of a stock item differs from the confirmed stock record
balance by 10 percent or more. A minor difference exists
if the count differs less than 10 percent. All ships treat
inventory differences for SPECIAL MATERIAL, listed
in the previous paragraphs, as major differences.
Preliminary Research
The preliminary research consists of checking
recent transactions, unposted or rejected docu-
mentation, and temporary locations. It also includes
verifying catalog data, such as unit of issue, quantity per
unit pack or other data.
Causative Research
This is an in-depth investigation of specific
inventory discrepancies. Causative research is con-
ducted to determine the cause of the inventory
discrepancy so corrective action can be taken. This
consists of a complete review of all transactions, within
the allowable look-back period, in the history files. The
transactions that need review are the receipts, change
notices, expenditures, location updates, and unposted or
errored documents. Normally, causative research is
conducted after posting the inventory adjustment to the
stock record. The research should be completed within
30 days from the date the adjustment was posted to the
stock record. The supply officer reviews the results of
causative research periodically. Also, the supply officer
initiates actions to prevent recurrence of such inventory
discrepancies.
Posting Inventory Results
The procedures for posting the result of physical
inventories may vary from each activity. Posting
depends upon the method or equipment used by the
activity. Activities using the manual procedures use the
Stock Record Card Afloat, NAVSUP Form 1114.
Activities using automated procedures may process the
results by using the inventory function in the computer
program. After posting, file the inventory count
documents in the stock control history file in NIIN
sequence. Keep the completed count documents in file
10-12
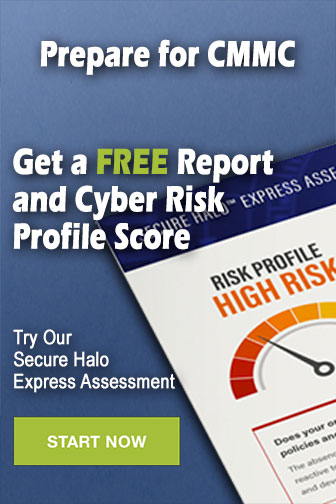