. When a random sampling inventory of that
storeroom fails to meet the inventory accuracy rate of
90 percent.
. When directed by the type commander
(TYCOM) before a supply management inspection
(SMI).
. When directed by the commanding officer (CO).
. When circumstances clearly shows that it is
required for effective inventory control.
SPECIFIC COMMODITY INVENTORIES
Specific commodity inventories are physical counts
of all items of generic segments of material. For
example, this would include an inventory of material
under the same cognizance symbol. This type of
inventory is taken under the same conditions as a
bulkhead-to-bulkhead inventory. However, this type of
inventory requires prior knowledge of specific stock
numbers and item locations.
SPECIAL MATERIAL INVENTORIES
Special material inventories require the physical
count of all items, which because of their physical
characteristics, cost, mission essential status, criticality,
or other reasons, are specifically designated for separate
identification and inventory control. Special material
inventories include, but are not limited to, stocked items
designated as classified or hazardous. Special material
inventories also include controlled equipage and
presentation silver. Physical inventories of such
material are required on a scheduled basis as prescribed
in chapter 6 of NAVSUP P-485.
Classified Items
Classified items require an inventory annually and
upon change of custodial responsibility. Security codes
identify classified items in stock records. See the listing
of security codes in appendix 9 of NAVSUP P-485.
Hazardous Items
Perform physical inventory of hazardous items
annually. During the inventory, carefully inspect each
unit of every item for material condition, correct
identification, and proper marking or labeling.
Depot-Level Repairable
Inventory aviation depot-level repairable (AVDLR)
items annually. After completing the inventory, turn in
all repairable identified as excess to the nearest ashore
supporting activity. Induct those repairable requiring
condition tags to the supporting maintenance for test,
check or repair. Items not in the stock record must be
taken up in stock after adding the information in the
stock record. Before adding information to the record,
stock control should completely research these items to
avoid duplication or erroneous records.
Other Materials
Other stock items that may be specifically
designated by the inventory manager, fleet commander,
TYCOM, or the CO for special inventory control should
be inventoried according to the frequency
established by the directing authority.
Shelf-Life Items
criteria
Deteriorative shelf-life items, other than those
included in the items just discussed, are not required to
be periodically inventoried, but must be screened as
often as necessary to ensure timely use or transfer before
their shelf-life expiration date.
SPOT INVENTORIES
Spot inventories are unscheduled physical
inventories taken to verify the existence of specific stock
items. A spot inventory is taken as a result of the
following:
. When the request shows total not in stock (NIS)
but the verified stock record for the requested item
shows anon-hand balance.
. When issue transaction is a partial NIS issue and
stock record shows that anon-hand balance is more than
the issued quantity.
. To determine the on-hand quantity of a particular
item when and as requested by the CO, TYCOM,
cognizant inventory manager, or other competent
authority.
An example of a spot inventory is when the CO
requests the physical inventory of an item that he or she
considers to be highly essential to prospective
operations. Another example is when the type
commander needs to have total asset visibility of a
particular critical item.
10-10
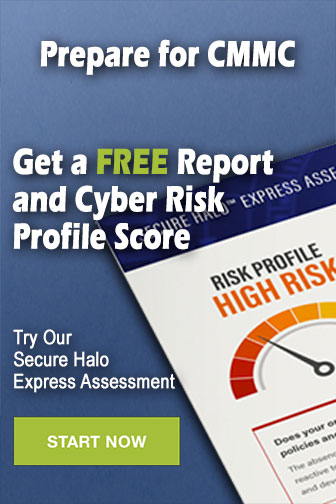