The rule depth gage is a graduated rule with a
sliding head designed to bridge a hole or slot and to
hold the rule perpendicular to the surface on which
the measurement is taken. This type has a measuring
range of 0 to 5 inches. The sliding head has a
clamping screw so it may be clamped in any position.
The sliding head has a flat base that is perpendicular
to the axis of the rule and ranges in size from 2 to 2
5/8 inches in width and from 1/8 to 1/4 inch in
thickness.
The micrometer depth gage consists of a flat base
attached to the barrel (sleeve) of a micrometer head.
These gages have a range from 0 to 9 inches,
depending on the length of extension rod used. The
hollow micrometer screw (the threads on which the
thimble rotates) itself has a range of either 1/2 or 1
inch. Some have a ratchet stop. The flat base ranges
in size from 2 to 6 inches. Several extension rods are
normally supplied with this type of gage. To measure
the depth of a hole or slot with reasonable accuracy,
use a depth gage as shown in figure 2-48, view A.
Hold the body of the depth gage against the surface
from which the depth is to be measured and extend
the scale into the hole or slot. Tighten the set-screw
to maintain the setting. Withdraw the tool from the
work and read the depth on the scale.
To measure the depth of a hole or slot with more
accuracy than is possible with an ordinary depth
gage, place a vernier depth gage over the slot as
shown in figure 2-48, view B. Notice the clamping
screws are at X and Y; the horizontal adjusting screw
nut is at Z. With X and Y loose, slide the scale down
into the slot being measured until it is almost in
contact. Then tighten X to make Z operative. With Z,
adjust the scale to the proper feel and secure the
setting with Y. By proper feel we mean the
adjustment at which you first notice contact between
the end of the scale and the bottom of the slot. Then
read the setting as described under Reading a
Vernier Scale.
To set the vernier depth gage to a particular
setting, loosen both setscrews at X and at Y and slide
Figure 2-48.Using depth gages.
the scale through the gage to the approximate
setting. Tighten the sets crew at X, turn the knurled
nut at Z until the desired setting is made, and tighten
the setscrew at Y to hold the setting.
To measure the depth of a hole or slot, as shown
in figure 2-48, view C, with more accuracy than is
possible with either an ordinary depth gage or a
vernier depth gage, place a micrometer depth gage
over the slot and adjust the thimble until the contact
of the spindle causes the ratchet stop to slip. Remove
the micrometer from the work and read the
micrometer. Remember, if extension rods are used,
the total depth reading will be the sum of the length
of the rods plus the reading on the micrometer.
DIAL INDICATOR
The dial indicator is used in several different
ways to measure the amount of deviation (or runout)
in revolving or rotating parts. Accurate shaft-to-shaft
alignment is impossible without using a dial
indicator.
Dial indicators are supplied with various fittings,
links, and adapters. Additionally, special application
hardware is available. Figure 2-49 illustrates the
basic hardware of a dial indicator set and two
different types of dial heads. The dial scale is usually
graduated in thousandths of an inch and has an
adjustable bezel around it. The scale of a dial
indicator usually reads plus numbers to the right of
zero and minus numbers to the left of zero.
The typical setup for checking the trueness of a
shaft, using a dial indicator and vee blocks (or roller
blocks), is to place the shaft in the vee blocks, mount
the magnetic base or clamp attachment (whichever is
the most appropriate) with the swivel post and dial
head attached to a solid surface. Adjust the mounting
linkage to a convenient angle that permits ease in
reading the dial (but does not interfere with the task
being performed). Bring the sensor button into
contact with the shaft, loosen the swivel post clamp
screw, raise and lower the sensor button to determine
what the full travel of the indicator is. After the
extent of travel has been determined, set the pointer
at mid travel, secure the swivel post clamp screw, and
then zero the dial with the adjustable bezel. Rotate
the shaft slowly and observe the pointer for deviation.
The combined deflection (plus and minus sides of the
scale) is the total indicator reading (TIR).
CARE OF PRECISION INSTRUMENTS
Special treatment is required for precision
instruments if they are to serve their intended
purpose. The following precautions will help ensure
their accuracy.
2-30
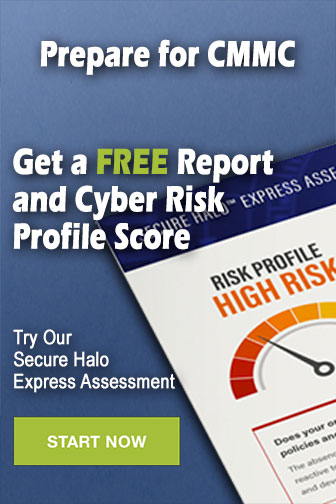