CHAPTER 4
AIRCRAFT BASIC CONSTRUCTION
INTRODUCTION
Naval aircraft are built to meet certain specified
requirements. These requirements must be selected so
they can be built into one aircraft. It is not possible for
one aircraft to possess all characteristics; just as it isn't
possible for an aircraft to have the comfort of a
passenger transport and the maneuverability of a
fighter. The type and class of the aircraft determine how
strong it must be built. A Navy fighter must be fast,
maneuverable, and equipped for attack and defense. To
meet these requirements, the aircraft is highly powered
and has a very strong structure.
The airframe of a fixed-wing aircraft consists of the
following five major units:
1.
Fuselage
2.
Wings
3.
Stabilizers
4.
Flight controls surfaces
5.
Landing gear
A rotary-wing aircraft consists of the following
four major units:
1.
Fuselage
2.
Landing gear
3.
Main rotor assembly
4.
Tail rotor assembly
You need to be familiar with the terms used for
aircraft construction to work in an aviation rating.
STRUCTURAL STRESS
LEARNING OBJECTIVE: Identify the five
basic stresses acting on an aircraft.
The primary factors to consider in aircraft
structures are strength, weight, and reliability. These
factors determine the requirements to be met by any
material used to construct or repair the aircraft.
Airframes must be strong and light in weight. An
aircraft built so heavy that it couldn't support more than
a few hundred pounds of additional weight would be
useless. All materials used to construct an aircraft must
be reliable. Reliability minimizes the possibility of
dangerous and unexpected failures.
Many forces and structural stresses act on an
aircraft when it is flying and when it is static. When it is
static, the force of gravity produces weight, which is
supported by the landing gear. The landing gear absorbs
the forces imposed on the aircraft by takeoffs and
landings.
During
flight,
any
maneuver
that
causes
acceleration or deceleration increases the forces and
stresses on the wings and fuselage.
Stresses on the wings, fuselage, and landing gear of
aircraft are tension, compression, shear, bending, and
torsion. These stresses are absorbed by each component
of the wing structure and transmitted to the fuselage
structure. The empennage (tail section) absorbs the
same stresses and transmits them to the fuselage. These
stresses are known as loads, and the study of loads is
called a stress analysis. Stresses are analyzed and
considered when an aircraft is designed. The stresses
acting on an aircraft are shown in figure 4-1.
TENSION
Tension (fig. 4-1, view A) is defined as pull. It is the
stress of stretching an object or pulling at its ends.
Tension is the resistance to pulling apart or stretching
produced by two forces pulling in opposite directions
along the same straight line. For example, an elevator
control cable is in additional tension when the pilot
moves the control column.
COMPRESSION
If forces acting on an aircraft move toward each
other to squeeze the material, the stress is called
compression. Compression (fig. 4-1, view B) is the
opposite of tension. Tension is pull, and compression is
push. Compression is the resistance to crushing
produced by two forces pushing toward each other in
the same straight line. For example, when an airplane is
on the ground, the landing gear struts are under a
constant compression stress.
4-1
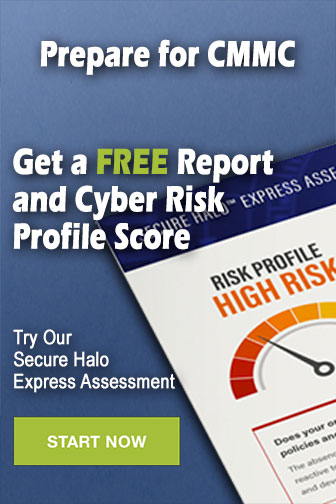