Figure 7-23 shows the three phases of pump
compensation in a pressure buildup order, starting at
low pressure and increasing to full system pressure.
As shown in view (A), the yoke control piston is
spring loaded to hold the displacement yoke at its
maximum displacement angle of 30 degrees. This
spring is opposed by the existing system pressure,
which acts at all times on the constant horsepower
piston area; however, the hydraulic force will not be
sufficient to move the yoke control piston until the
actuating pressure (system pressure) builds up to
2,200 psi. Thus, the cylinder block will be canted to
its maximum angle, and the pump will deliver its
maximum flow, 8 gpm, when system pressure is less
than 2,200 psi.
View (B) of figure 7-23 shows how the yoke con-
trol piston responds to system pressure fluctuations in
the 2,200 to 2,950 psi range. Assuming that system
pressure is steadily increasing, the displacement yoke
angle will decrease from the 30-degree full
displacement angle to approximately 22 degrees,
which will produce 6 gp at 2,950 psi.
View (C) of figure 7-23 shows how the spring
load on the compensator spool is overcome by system
pressure in excess of 2,950 psi, and the displaced
spool meters pressure to the "cutoff" area of the yoke
control piston.
This pressure will act with the
constant hp force on the piston, and with increasing
pressure, the piston will move rapidly from the
22-degree displacement angle at 2,950 psi to
approximatey 0 degrees at 3,000 (plus 150, minus 0)
psi.
When full pressure exists, the hydraulic power
output will be the minimum required to replace fluid
that leaks internally. The gearbox installed between
the motor and pump contains lubricating fluid for
internal lubrication, a dipstick for checking its fluid
level, fill port to replace fluid, drain port to drain fluid
during maintenance, and a relief valve to allow excess
fluid to be relieved overboard. The pump gearbox is
drained and reserviced with clean hydraulic fluid as
follows:
1. Remove the magnetic drain plug and catch the
fluid in a suitable container.
2. Inspect the magnetic plug for foreign particles
that may have accumulated during periods of
operation. Particles that look and feel like fuzz are
considered acceptable; however, particles containing
metal slivers require pump overhaul.
3. Remove the filler plug, and flush the gearbox
with hydraulic fluid.
4. Clean the magnetic plug, install with a new
gasket, and lockwire after replacing.
5. Refill gearbox with hydraulic fluid.
6. Install filler plug and dipstick, using new
gaskets.
Also, the pump pressure line, fitting, and filter
screen are removed. The filter screen is cleaned,
using Dry-Cleaning Solvent P-D-680, and reinstalled
using a new gasket.
The pump pressure line is
reinstalled and an operational check performed.
NOTE: Hydraulic pumps that are not
functioning properly can represent a serious
source of contamination in an operating
hydraulic system. Hydraulic contamination
is discussed in chapter 4 of this TRAMAN.
RELIEF VALVES
Relief valves are not new to most people;
different types of relief valves are used in our homes
and automobiles, as well as many other places. Relief
valves are pressure limiting or safety devices
commonly used to prevent pressure from building up
to a point where it might blow seals or burst or
damage the container in which it is installed, etc.
In aircraft, relief valves are installed within
hydraulic systems to relieve excessive pressurized
fluid caused from thermal expansion, pressure surges,
and the failure of a hydraulic pumps compensator or
other regulating devices.
Main System Relief Valves
Main system relief valves are designed to operate
within certain specific pressure limits and to relieve
complete pump output when in the open position.
Relief valves are set to open and close at
pressures determined by the system in which they are
installed. In systems designed to operate at 3,000 psi
normal pressure, the relief valve might be set to be
completely open at 3,650 psi and reseat at 3,190 psi.
These pressure ranges may vary from one aircraft to
another. When the relief valve is in the open position,
it directs excessive pressurized fluid to the reservoir
return line.
7-22
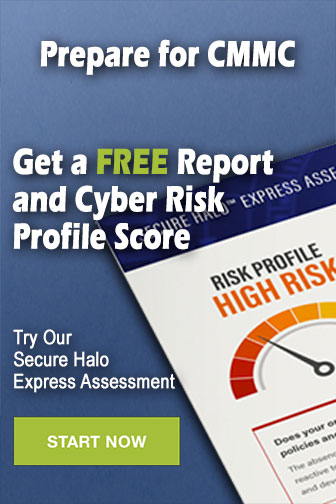