pressure compensator cylinder, where it moves the
compensator piston against the force of the calibrated
control (compensator) spring. This motion,
transmitted by a direct mechanical linkage, moves
sleeves axially on the piston, thereby varying the time
during which relief holes are covered during each
stroke.
Fluid flows through the hollow pistons during the
forward stroke and escapes out the relief holes until
they are covered by the piston sleeves. The effective
piston stroke (delivery) is controlled by the piston
sleeve position. During nonflow requirements, only
enough fluid is pumped to maintain system pressure
against leakage.
During normal pump operation, three conditions
may existfull flow, partial flow, and zero or
nonflow. During full flow operation (fig. 7-20), fluid
enters the intake port and is discharged to the
high-pressure side past the pump checks by the
reciprocating action of the pistons. Piston sleeves
cover the relief holes for the entire pressure stroke.
During partial flow, system pressure is sufficient
(as bled through the orifice) to move the compensator
stem against the compensator spring force.
If system pressure continues to build up, as
under nonflow conditions, the stem will be moved
further until the relief holes are uncovered for
practically the entire piston stroke. Relief holes
will be covered only for the stroke necessary to
maintain pressure against system leakage and to
produce adequate bypass flow.
Bypass.The bypass system is provided to
supply self-lubrication, particularly when the pump is
in nonflow operation. The ring of bypass holes in the
pistons are aligned with the bypass passage each time
a piston reaches the very end of its forward travel.
This pumps a small quantity of fluid out the bypass
passage, back to the supply reservoir, and provides a
constant changing of the fluid in the pump. The
bypass is designed to pump against a considerable
back pressure for use with pressurized reservoirs.
Maintenance. Line maintenance of the
Stratopower pump is limited to operational checks,
and checking for leaks and loose fittings.
Malfunctioning pumps should be removed and
replaced.
In removing a pump, always maintain its
alignment until the drive shaft is fully withdrawn
from the driving element. Never pick up or carry a
pump by the drive shaft extension.
Before installing a pump, the pump and its
attached hose assemblies must be primed (filled with
fluid).
During installation, the pump must be
continuously supported with its shaft parallel to the
mounting studs, and the splines must mesh with the
driving element.
If the pump drive shaft does not engage the
driving element, preventing the pump from sliding
into place, the drive shaft should be manually rotated
until the two splined drive shafts mate.
PISTON-TYPE PUMP (VICKERS ELEC-
TRIC MOTOR-DRIVEN VARIABLE DIS-
PLACEMENT).This type of pump is used in some
of the Navys most modern aircraft. Motor-driven
variable displacement pumps have several advantages
over the engine-driven models. Some of these
advantages are as follows:
1. Ease of installation and removal due to the
accessibility of the component.
2. Constant speed of the drive shaft.
3. Eliminates the need of using a test stand to
drop check the landing gear and perform operational
checks of other actuating systems.
NOTE: Hydraulic test stands are seldom
used on aircraft that incorporate this type of
pump because foreign particles could be
transferred from the test stand to the aircraft,
thus contaminating the hydraulic system.
4. The pump assembly contains an internal
centrifugal boost pump, which provides a positive
fluid pressure at the suction port of the variable
displacement pump.
The only disadvantages of the pump are the size
of the complete assembly and its weight. For this
reason, this type of pump is used in patrol and
transport aircraft.
7-19
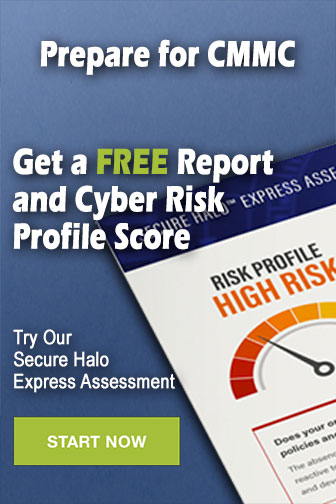