The main parts of the pump are the drive shaft,
pistons, cylinder block, and valve plate. There are
two ports in the valve plate. These ports connect
directly to openings in the face of the cylinder block.
Hydraulic fluid is sucked in one port and forced out
the other port by the reciprocating (back-and-forth)
motion of the pistons.
There is a fill port in the top of the cylinder
housing. This opening is normally kept plugged, but
it can be opened for testing the pressure in the housing
or case.
When you install a new pump or newly
repaired one, this plug must be removed and the
housing filled with fluid before the pump is operated.
There is a drain port in the mounting flange to drain
away any leakage from the drive shaft oil seal.
When the drive shaft is rotated, it rotates the
pistons and cylinder block with it. The offset position
of the cylinder block causes the pistons to move back
and forth in the cylinder block while the shaft,
pistons, and cylinder block rotate together. As the
pistons move back and forth in the cylinder block,
they draw the fluid in one port and force it out the
other. This action creates a steady, nonpulsating flow
of fluid. Certain models of this pump are capable of
developing up to 3,000 psi working pressure.
Constant displacement pumps of this series are
designed so they can be driven in either direction.
The direction of rotation of the pump must coincide
with the engine accessory section. The pump rotation
can be determined by referring to an arrow on the
pump housing adjacent to the valve plate. The only
change necessary when changing the direction of
rotation of the pump is to rotate the valve plate 180
degrees.
Before installation, the pump mounting flange
and shim, if used, must be wiped clean. The pump
must be primed by filling the housing with hydraulic
fluid through the fill port. The exposed drive shaft
spline should be lubricated. To ensure internal
cleanliness, the shipping plugs should not be removed
until the lines are ready for attachment.
Normally, for repair, the pump should be shipped
to an intermediate-level activity; however,
replacement of packings and gaskets can be
accomplished in the field. To prevent damage in the
event of the pump binding, a shear section is
incorporated in the drive shaft coupling.
The
coupling may be replaced if the cause of the shearing
is known and has been remedied. Immediately after
removal, the pump housing should be filled
two-thirds full with hydraulic fluid; the drive shaft
couplings should be suitably protected by a wood
block; and the ports securely plugged to prevent the
entrance of foreign matter.
PISTON-TYPE PUMPS (STRATOPOWER
VARIABLE
DISPLACEMENT).There
are
several models of the Stratopower variable
displacement pump currently used on naval aircraft;
however, all are similar in principle of operation, The
pump described here is a Model 65 WB06006, rated at
3,000 psi and capable of delivering 13 gallons of fluid
per minute at 3,800 rpm.
Pressure regulation and flow control are
accomplished internally, automatically adjusting
pump delivery to meet the system demands.
Flow cutoff begins at approximately 2,850 psi,
and it reaches zero (unloads) at 3,000 psi. When the
pump is operating in the unloaded condition, the
bypass system provides circulation of fluid internally
for cooling and lubrication of the pump.
The pump has three portsthe suction port, the
discharge port, and the drain or bypass port. The
latter port is connected to the reservoir return line.
The pump is driven from the engine accessory drive
by a splined drive coupling. A shear section is
provided in the pump drive shaft to prevent damage
from overload. Figure 7-16 shows the internal
features of the pump.
Four major functions are performed by the
internal parts of the pump. These functions are
mechanical drive, fluid displacement, pressure
control, and bypass.
Mechanical Drive Mechanism.The mechani-
cal drive mechanism is shown in figure 7-17. Piston
motion is caused by the drive cam displacing each
piston the full height of the drive cam each revolution
of the drive shaft. By coupling the ring of pistons
with a nutating (wobble) plate supported by a fixed
center pivot, the pistons are held in constant contact
with the cam face. As the drive cam depresses one
side of the nutating plate (as pistons are advanced),
the other side of the nutating plate is withdrawn an
equal amount, moving the pistons with it. The two
creep plates are provided to decrease wear on the
revolving cam.
Fluid Displacement.A schematic diagram of
the displacement of fluid is shown in figure 7-18.
Fluid is displaced by axial motion of the pistons. As
each piston advances in its respective cylinder block
7-16
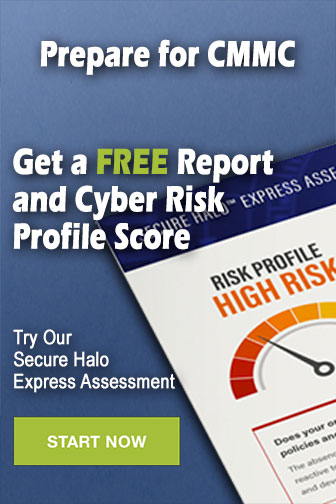