protected during shipment with a sprayable, strippable
coating system that conforms to MIL-C-6799, type II.
Normally, type II coatings are safe on metal, plastic,
or painted surfaces. Also, they are useful for protecting
clear acrylic surfaces, such as canopies, against
abrasion during maintenance or extended periods of
downtime.
The type II system consists of a black base coat
and a white topcoat that provides heat reflection during
outside exposure. Nylon ripcords with finger-size
loops are placed about the aircraft before the aircraft
is sprayed with this coating. This allows manual
stripping of coatings. When properly applied, the
coatings can be removed easily. If coatings are sprayed
too thin for easy removal, they can be recoated and
allowed to dry. The top layer will bond to previous
layers, and all layers may be manually stripped in one
operation.
Corrosion-Preventive Petroleum
(MIL-C-11796)
MIL-C-11796 is designed for hot application. It is
available in two classes, class 1 (hard film) and class
3 (soft film). Both classes consist of corrosion
inhibitors in petroleum. They are removed with
Stoddard solvent or mineral spirits. Where a hard film
is not necessary, you should use class 3. Class 3 is
easier to apply and remove, yet it gives the same
degree of protection as class 1. Class 1 is for long-time,
indoor protection of highly finished metal surfaces and
aircraft control cables. Class 3 provides protection for
metal surfaces, such as antifriction bearings,
shock-strut pistons, and other bright metal surfaces.
Class 1 must be heated to 170°F to 200°F before it is
applied by brush or dip. For brushing, class 3 material
must be between 60°F and 120°F, and for dipping,
between 150°F and 180°F.
Oil, Preservative, Hydraulic Equipment
(MIL-H-46170)
Use hydraulic fluid MIL-H-46170 as a
preservative fluid to store hydraulic systems and
components. It is also used as a testing medium in
stationary test stands within a temperature range of
-40°F to +275°F. Hydraulic fluid MIL-H-46170 is
NOT to be used in portable test stands that are
connected to the aircraft.
This hydraulic fluid is a fire-resistant, synthetic,
hydrocarbon, hydraulic fluid similar to MIL-H-83282.
MIL-H-46170 is used as a preservative fluid in
systems operating on MIL-H-83282.
Lubrication Oil, General-Purpose,
Preservative
There are several types of lubricating oils, some
of which contain preservatives. Each oil is identified
by a specification number. Use the correct oil for each
situation. The specification number for the oil
described in this section is VV-L-800.
VV-L-800 oil is used to lubricate and protect
piano-wire hinges and other critical surfaces. It is also
used when a water-displacing, low-temperature,
lubricating oil is required. You may apply VV-L-800
as received by brush, spray, or dip. It is readily
removed with dry-cleaning solvent or mineral spirits.
Corrosion-Preventive Compound
(MIL-C-81309)
MIL-C-81309 corrosion-preventive compound is
a water-displacing compound and lubricant that must
be reapplied frequently. On exposed surfaces,
protection lasts about 7 days at best. On internal areas,
protection lasts about 30 days. MIL-C-81309 is
available in two typestype II and type III.
Type II is used for external areas. It forms an
effective barrier against moisture when used on
B-nuts, linkages, bolts, nuts, ejection seat
mechanisms, and canopy locks. When you lubricate an
area where there are no pressure lubricating fittings
(zerk fittings), such as the piano hinges on access doors
and control surfaces, spray with type II preservative
compound to clean the area before you apply
VV-L-800 preservative oil to remove moisture and
contaminants.
Type III corrosion-preventive compound is for
avionics and electrical equipment usage. It is not for
use on exterior areas that will be exposed to the
environment. Type III is used primarily on electrical
connectors (cannon plugs) and microswitches to
remove moisture and contaminants and to prevent
corrosion.
Packaging and Barrier Materials
A minimum of packaging is necessary at the
operating activity level. However, critical aircraft and
engine areas require shrouding against contamination
during maintenance and repair. The fuselage must be
sealed when cleaning and stripping materials are used
4-17
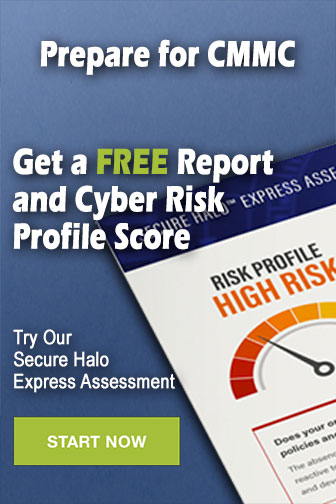