vapor leak will not affect the performance of the
pump; no particular effort need be made to
eliminate a leak unless it reaches the point at which
it becomes visible. If a leak should develop at the
lower end of the plunger, tighten the plunger
guide, shown in figure 3-8, with a rod (approx-
imately 3/8 inch by 6 inches). Do not bind the
plunger by tightening it too snugly. When you can
no longer adjust the tightness of the plunger guide,
remove the compressor body from the frame and
insert new packing as follows:
1. Unscrew the four bolts that hold the
compressor body to the crosshead guide and
remove the pin that holds the plunger to the
crosshead.
Figure 3-8.Compressor assembly of the Walter Kidde CO2
transfer unit.
2. Place the compressor body in a vise and
remove the plunger guide and old packing. Insert
only the two large pieces of packing and the
spacer. Then insert the plunger guide and turn it
down as far as possible to compress and form the
packing around the plunger. This operation will
cause the plunger to bind, but you can free it by
turning and working the plunger up and down a
few times.
3. Remove the plunger guide and insert the
small ring of the packing. Install the packing so
that the level fits the packing already in place and
the plunger guide. Replace the plunger guide and
turn it in until the maximum dimension between
the body at point (A) and the end of the plunger
guide (B) (figure 3-8) is 1 3/16 inches. If the
plunger guide is not screwed in sufficiently, the
crosshead will strike the plunger guide. To free
the plunger, work it back and forth several times.
4. Replace the compressor body and extend
the plunger so that it can be lined up with the
crosshead and the pin being replaced. After you
connect the end of the plunger with the crosshead,
which may have had to be moved to its top
position to accomplish the connection, tighten the
bolts securely. Turn the master gear several
revolutions by hand to make sure the crosshead
does not strike the plunger guide.
Safety Disc
Figure 3-4 and 3-5 illustrate the safety disc
arrangement located in the discharge body. The
method of removal and replacement of the
safety disc is self-evident in the illustration;
however, never use a disc that is stronger or
weaker (tensile strength capacity) than specified.
Cleaning
No foreign matter should be in the areas of
recharging pump connections. If a decrease is
noted in the amount of carbon dioxide trans-
ferred (it should be approximately 80 percent of
the supply cylinder), remove the two check valves
(figure 3-5) in the compressor head and clean
them. To do this, remove the discharge head body
(right-hand thread). Then remove two screws and
the retaining wire. The inlet check will then be
accessible. You can remove the outlet check by
unscrewing the plug. Clean both checks and the
seat thoroughly.
The strainer on the inlet line (from the
supply cylinder) should be cleaned frequently for
maximum efficiency of the pump.
3-10
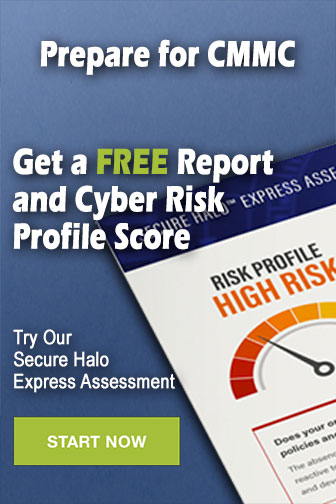