aircraft and the specific location of the damage on the
aircraft.
Class I
Class II
Class III
Class IV
Class V
Class VI
Class VII
Cuts, scratches, pits, erosion or
abrasions not exceeding 0.005 inch
in depth and 5 inches in length.
Damage with dents in the skin up to
3 inches in diameter and 0.01 inch in
depth, with no delamination
between skin plies, no cracks or
graphite fiber breakage, or skin to
honeycomb core separation.
Delamination between plies,
including the skin land area, opened
up to external edge and up to 1 1/2
inches in diameter.
Skin damage including delami-
nation, cracks, cuts, scratches or
skin erosion exceeding 0.015 inch
in depth, but less than full
penetration, with no damage to
honeycomb core.
Damage is single skin damage,
including full penetration, accom-
panied with honeycomb core
damage.
Damage to both skins, including full
penetration, accompanied with
honeycomb core damage.
Damage is water trapped in honey-
comb area.
REPAIR CRITERIA
Repair criteria differ in the same way that initial
design requirements for aircraft differ. Criteria for a
repair can be less demanding if the repair is
considered to be temporary. Temporary repairs are
performed for such requirements as a onetime flight
to a repair facility or one more mission under combat
conditions. However, most repairs are intended to be
permanent, and, except for special conditions, criteria
are applied so that the repair will remain acceptable
for the life of the aircraft.
One of the major factors that influences the repair
quality is the environment where the repairs are to
made. For example, the presence of moisture is
critical to bonded repairs. Epoxy resins can absorb
1.5 to 2 times their weight in moisture, thereby
reducing the ability of the resins to support the fibers.
Dirt and dust can seriously affect bonded repairs.
Oils, vapors, and solvents prevent good adhesion in
bonded surfaces and can lead to voids or
delamination. To perform quality repairs, personnel
must have a knowledge of the composite system to be
repaired, type of damage, damage limitations/
classifications, repair publications, materials, tools
and equipment, and repair procedures.
The repair facilities where the work is to be
performed will be clean and climate controlled if
possible. The relative humidity should be 25 percent
to 60 percent and temperatures stable at 65° to 75°F.
If repairs are to be made in an uncontrolled
environment (hangar/flight deck), patches and
adhesives will be prepared in a controlled
environment and sealed in an airtight bag before
being brought to the repair site.
Strength Restoration
Full strength repairs are desirable and should be
made unless the cost is prohibitive or the facilities are
inadequate.
Less than full strength repairs are
sometimes allowed on secondary structures that are
lightly loaded, stiffness-critical structures designed
for limited deflections rather than for carrying large
loads (doors), or structures designed to a minimum
thickness requirement for general resistance to
handling damage (fuselage skins). Repair manuals
for specific aircraft frequently zone the structure to
show the amount of strength restoration needed or the
kinds of standard repairs that are acceptable. Repair
zones help to identify and classfy damage by limiting
repairs to the load-carrying requirements.
Repair
zone borders indicate changes in load-carrying
requirements due to changes in the structure, skin
thickness, ply drop-offs, location of supporting
members (ribs and spars), ply orientation, core
density, size and type of materials. Damage in one
zone may be repairable, where as the same type of
damage in an adjacent zone may not be repairable.
See figure 14-27.
Aerodynamic Smoothness
High-performance aircraft depend on smooth
external surfaces to minimize drag. During initial
fabrication, smoothness requirements are specified,
usually by defining zones where different levels of
aerodynamic smoothness are required. These most
14-26
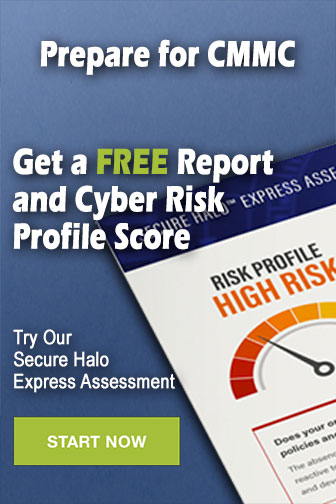