afloat. Also, the Aviation Supply Office (ASO)
publication C0030 provides packaging data for aviation
repairable assemblies. During delivery, material must be
properly loaded and secured in the vehicle to prevent
damage from falling or jolting.
All material for issue will have documentation. The
material will have at least two copies of the issue
documents. One copy for the customer and one signed
copy as proof of delivery.
Issues Afloat
This section provides issue procedures for general
use consumables, repair parts, and repairable. The
basic rule for issuing material afloat is the same as for
shore sites. That is, the authority for issuing material
afloat is also a request from the customer. Upon receipt
of the requisition, the supply activity processes it fix
issue or referral and provides status to the customer.
Upon delivery of material, the customer signs and put
the current date on the issue document. The customer
retains one copy of the issue document as record of the
completed requisition. Delivery personnel forward the
signed copy of the issue document to the stock control
branch or supply response section for use as proof of
delivery.
Whether the ship uses the manual or mechanized
procedures, the NAMP processing standards still apply.
Refer to Table 7-1 for the processing standards.
Under mechanized procedures, activities can
submit material requirements on-line by using a
computer. The Shipboard Uniform Automated Data
Processing System-Real Time (SUADPS-RT) provides
this function. Aviation activities use the Naval Aviation
Logistics Command Management Information System
(NALCOMIS) procedures. Entries in the customer
identification and user identification files control access
to this function in the computer. Refer to SUADPS-RT
support procedures and NALCOMIS publications for
use of this function.
The term off-line, used by supply onboad ships,
refers to manual processing. In off-line processing, the
customer submits requisitions on a locally approved
form to the supply response section or customer service.
The requisitions must contain, at a minimum, the
following information:
NSN/NICN/LICN or part number
Unit of issue
Quantity
Document number
Chargeable end-use fund code
Project code
Priority
Advice code, if applicable
MDS data, if applicable
Cognizance symbol (NC items only)
Nomenclature (NC items only)
Supply personnel may process the requisitions
received off-line into SUADPS-RT or completely
off-line if necessary. At the first opportunity, supply
personnel can process issues processed off-line in
SUADPS-RT by using the post-post option.
MECHANIZED PROCESSING. Upon sub-
mission, SUADPS-RT automatically compares the
material requests entered via computer to the control
and validation files. This validation process allows for
entering only the valid data in the system. Validation
errors will cause an error message, and will require
correction to continue processing. Upon completion of
the validation process, SUADPS-RT will produce an
issue document for available material. Storage
personnel use the issue document to locate, pickup, and
deliver material. The issue document lists up to four
locations of the material. Storage personnel must search
these locations to find the material for issue. If needed,
a list of additional locations maybe available in location
files.
There are several types of transactions involved
when you operate under SUADPS-RT. They are
complete issue, standard pack adjustment, partial issue,
or not in stock (NIS).
The term complete issue refers to the issuance of the
complete quantity requested (fig. 7-1). When processing
the issue document, personnel making the issue must
circle the quantity issued on the document and attach
one copy to the material. Personnel may use the FIRST
DESTINATION ADDRESS of the issue document for
the staging area location, name, and date. Upon delivery
of material, the customer signs and date the issue
document.
Personnel making the issue must adjust the issue
quantity to coincide with the standard pack of the item.
To process the issue, line out the quantity requested and
enter and circle the quantity issued. Mark the issue
document with the words STANDARD PACK
ADJUSTMENT and deliver the material. See figure 7-2
for an example of issue with standard pack adjustment.
7-4
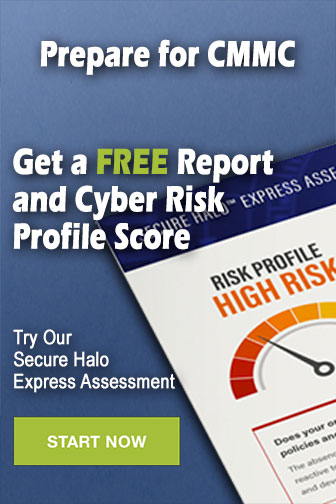