Types of Temporary Storage Facilities
The supply officer may designate the use of transit
sheds or butler huts to support the department's
functions. When used, they should provide the
safeguards, storage characteristics, and special storage
requirements needed for security purposes.
Pierside trailers may be used for the temporary
storage of supply department material when authorized
by the supply officer. The type of materials and security
requirements should be considered before using the
trailers.
When authorized, ships may also use other shore-
based facilities for temporary storage of material.
Identification of Temporary Storage Material
Material offloaded to shore activities for temporary
storage must be boxed, tagged, and marked to provide
ready identification. Each piece or container to be stored
must be numbered consecutively.
Documentation of Temporary Storage Material
The Requisition and Invoice/Shipping Document,
DD Form 1149, is used for material offloaded for
temporary storage. The form includes a notation
MEMORANDUM INVOICE ONLY in data block 4.
The next number from the expenditure invoice log is
assigned for control only. You must place one copy of
the DD Form 1149 inside each container. Also, you must
place one copy of the DD Form 1149 inside a waterproof
envelope securely attached to the outside of each
container. The DD Form 1149 must contain the
description, quantity, and classification of the material.
Also, it must have the type of storage required and the
length of time of temporary storage.
MATERIAL PROTECTION
Items procured for the Navy have some degree of
preservation packaging and packing that is required by
the item manager. The packaging should protect the
material from deterioration and damage during
shipment, handling, and stowage. The protection levels
specified are code-marked on unit packages and exterior
shipping containers. Level A provides protection
against the most severe conditions expected. Level B
provides protection for less severe conditions. Level C
provides protection for known favorable conditions.
Most materials received by afloat units are
packaged and packed before shipment. Ships personnel
are responsible for retaining repair parts in their original
packaging until issued. They are also responsible for
providing adequate protection of material while it is in
storage. Also, material must have adequate protection
during shipment. This includes shipment of unservice-
able, mandatory, turn-in repairable items to another
activity.
LOCATOR SYSTEMS
The stock locator system eases processing receipt,
issue, and shipment of material. The location of each
item in stock is recorded in the related stock record by
using manual or automated files. This record should
contain only as much information as necessary to find
the material. The stock locator file is the heart of a stock
location system. It is the address directory for all stored
material.
Locator Systems Ashore
Locator systems ashore are different and more
complicated than those afloat. To understand the locator
system ashore, you must understand storage layout,
location number format, and locator files.
The design of a locator system includes a
planograph. The planograph is a drawing of the actual
layout of a storage area. It portrays the subdivision of
the gross space within the storage space. A planograph
placed on the bulletin board enables the stock person to
match the location on the locator file with the floor plan.
The stock person may then proceed directly to the
location of the stored item.
The automated system in use today allows faster
response for inquiries concerning stock items. You must
learn the procedures for using these computers
according to your activitys instructions. Supply trans-
actions, such as receipts, issues, transfers, or surveys,
require posting into the computer system. The posted
transactions keep the information in the system current.
When stock numbers have more than one location
for small lots, the material should be combined into one
location. Combining material into one location requires
judicious planning. Usually, you can minimize
relocation of material through attrition. Transfer of
material between storeroom/warehouses or to different
locations in the same storeroom/warehouse requires
supervision by the leading storeroom AK. The leading
storeroom AK is responsible for the following:
Protecting the material from loss or damage
during the move
Ensuring proper stowage of material in the new
location
Ensuring prompt and accurate recording of new
locations into the stock records or files
STORAGE LAYOUT. Storage space ashore is
subject to considerable variations, depending upon the
6-4
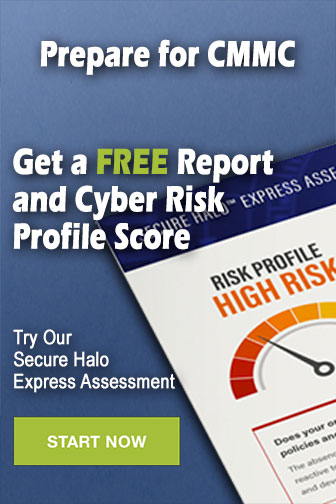