MATERIAL RECEIVED
Figure 5-11.-DD Form 1348-1 (Dummy Receipt).
WITHOUT PAPERWORK
The following texts describes the action needed for
processing material received without paperwork.
Dummy Invoice
Material received without paperwork needs
research. Use the information gathered from research to
prepare a dummy document and process the receipt.
Personnel in the receiving area perform the research and
prepare a dummy receipt on a DD Form 1348-1 (fig.
5-11) or DD Form 1149. The research includes checking
the requisition outstanding file by using available
information from the material. The information needed
are source of supply, stock or part number, i tern
description, document number, fund code, and location
(if for stock). When this information is known, enter the
quantity, date, and receipt signature on the dummy
receipt. You can then process the dummy paperwork as
a receipt. Keep dummy receipts in a separate stock
control history file.
Receipt Of Original Documentation
There will be occasions when you will receive the
original shipment paperwork after the material and
dummy invoice are processed. In these case, compare
the original paperwork and dummy invoice information.
If differences exists, corrector adjust posted records as
appropriate. Attach the original shipment paperwork
with the dummy invoice in the material completed file.
MATERIAL SAFETY DATA SHEET
The DOD Hazardous Material Information System
(HMIS) requires that a material safety data sheet
(MSDS) be completed for all hazardous material
purchased from commercial vendors. Hazardous
materials are those materials that, by virtue of their
potential y dangerous nature, require controls to assure
or vendor must identify hazardous material
of procurement. They must also package,
mark the material to provide the proper
at the time
pack, and
degree of
5-14
adequate safety to life and property. The manufacturer
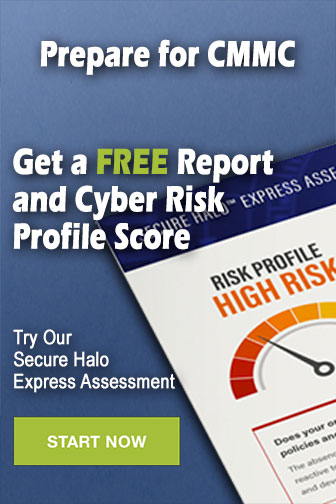