. Furnishes status to inquiring activities.
l Processes requirements for part numbered
material and provides analysis services for unidentified
material requests. Performs item research data
interpretation and selective item review tasks.
Under the RCC the Requisition Process Control
section performs the following functions:
. Receives, sorts, and processes requisitions
received by mail or message.
. Furnishes scheduled and special messenger
service throughout ASO on material requests document
matters.
. Routes and delivers lower priority requisitions to
other areas when such documents require manual
processing.
l Monitors, controls, and prepares reports on all
material requests and related documents that the branch
is processing.
The Part Number Requisition section of the
Requisition Control Center performs the following
functions:
l Provides analysis services for invalid, un-
identified, or non-stock numbered (non-NSN)
requisitions and inquiries.
. Conducts reviews for established source codes,
assigned stock number, approved alternate, or
replacement items.
. Recommends onetime procurement of non-NSN
items.
. Updates the document status file and provides
status on requisitions.
The Requisition Processing section performs the
following functions:
. Maintains records of all completed documents
(other than those retained on the document status tile).
l Processes follow-up requests submitted by
requiring activities.
l Furnishes priority HOT-LINE service to
customers.
The Expediting Services unit performs the
following functions:
. Pursues actions necessary to locate and provide
material to fill requisitions for stock numbered material.
. Identifies impending shortages in the supply
system (wholesale) material and acts to avoid or reduce
them.
. Interfaces with ASO Customer Advocates to
provide status on expected material availability for
customer requirements.
The Programs Management section performs the
following functions:
. Executes the Material Obligation Validation
(MOV) Program.
. Develops and reviews changes to requisition
processing procedures.
The Inventory Control Point (ICP)/Systems
Support Center of ASO Customer Operations performs
the following functions:
l Computes remaining outfitting retail material
requirements.
. Manages the execution of finds that finance
increases to retail supply levels.
. Maintains the currency of aviation depot-level
repairable (AVDLR) items wearout and survival data.
. Sets and monitors inventory levels of ASO
consumable items at selected operating activities.
. Ensures the timely provision of government-
furnished equipment (GFE) to meet weapons systems
production schedules.
The Industrial Support Center of ASO Customer
Operations is responsible for coordinating workload
projections with depot customers. It negotiates viable
repair schedules of AVDLR to provide maximum fleet
support. It also checks repair schedule change proposals
and revises organic and commercial rework schedules.
The Integrated Logistics Support (ILS) division
provides a complete range of technical functions
associated with provisioning of aeronautical
requirements. This division serves as liaison between
ASO and other activities on technically oriented
matters. Its responsibilities include determining the
technical characteristics of material for stock. The ILS
division has four branches. They are the ILS branch,
Provisioning branch, Cataloging branch, and Technical
Policy and Analysis branch.
The ILS branch processes Support Material List
(SML) of items with assigned stock number or
temporary Navy Item ControI Number (T-NICN).
1-6
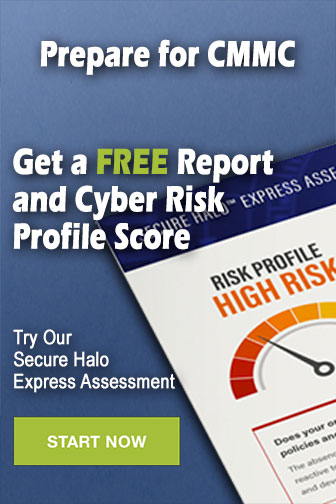