AND POSSIBLE DEATH! It is particularly important
to make sure that containers of poisonous liquids, such
as industrial alcohol, are clearly identified and labeled
to prevent human assumption, which can be fatal. The
most commonly used toxic substances on board ships
are pesticides.
HAZARDOUS MATERIAL SPILLS AND
EMERGENCIES
When using MHE or moving quantities of
hazardous materials between receiving, storage, and
issue, the possibility exists for spills and mishaps.
Some hazardous materials can cause severe health
hazards, burns to the skin and eyes, or give off toxic
gases. Spilled material can endanger the facility, the
ship, personnel, and the environment. Material Safety
Data Sheets (MSDSs) provide emergency spill
procedures, and every base or ship has spill contingency
plans and a spill response team in place should a mishap
occur.
Supply personnel should be trained on
emergency procedures should shipping containers fall
or break open, if material contacts personnel, or if a fire
occurs in a hazardous material area. Supply personnel
should also be trained in the use of safety equipment,
such as extinguishing systems, ventilation units,
personal protective equipment, and alarms.
MEASUREMENT OF STORAGE
SPACE
Measurement of a storage space is an important part
of planning the space layout for storage or office areas.
You will also use the standard measurements of bins,
pallet racks, pallets, and other storage items. Shore
activities are required to prepare and submit the Storage
Unit Report, NAVSUP Form 605. The Supply Ashore,
NAVSUP Publication 1, Volume 2, describes the
procedures for preparing the report. Although every
AK may not be involved in the actual preparation of the
report, you may be asked to provide some of the
information. The following information will help you
learn some of the terms and computations used in
storage operations.
TOTAL GROSS STORAGE AREA
Measure the total gross area by multiplying the
length by the width, in feet, of the inside dimensions of
the building. Measure from wall to wall and disregard
the inside structures such as fire walls, passageways,
ramps, stairwells, and so forth. The result will be the
square-foot area or total-gross area. The measurement
will be less than the outside dimensions by the thickness
of the walls.
Some storage buildings may have a cutback in the
walls or areas not designed for storage. The
measurement of the cutback is excluded from the total
gross area.
Open storage may be either improved or
unimproved. The total gross storage area must include
the entire own improved area. For an open unimproved
area, report only the area actually occupied by stores or
used in support of storage operations.
GROSS SPACE FOR STORAGE
OPERATIONS
To calculate the gross space for storage operations,
take the gross storage area minus the unusable space,
standby spare, and space outgranted to other DOD or
non-DOD activities.
NET STORAGE SPACE
To get the NET STORAGE SPACE (in feet), take
the total gross space for storage operations minus gross
space used for aisles, structural loss, and support spaces.
The result will be in square feet.
The aisles include the fire aisles, personnel access
aisles, main aisles, and cross aisles.
The structural losses are those areas not usable for
storage because of obstructions caused by their
characteristics. These include the pillars, posts, ramps,
door clearances, and fire walls. These also include the
spaces occupied by equipment such as electrical panels,
dehumidifiers, and so on. In open storage, structural
loss includes fire breaks and clearances for utility lines.
The support space is the gross space used in support
of storage operations. These spaces include shipping,
receiving, packing and preservation, and offices. Other
areas include MHE parking areas, battery charging
stations, rest rooms, locker rooms, and the time clock
area.
TOTAL CUBIC FEET CAPACITY
For covered storage, the total cubic feet is computed
by multiplying the net storage space (SQ FT) by the
stacking height. The stacking height is the distance
from floor to the unobstructed stacking height that is
permitted by safety regulations. See figure 2-8 for an
example of determining the cubic space capacity.
2-18
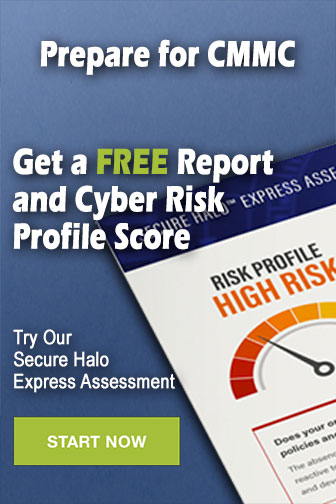