5510.1, for the proper handling of these materials.
Hazardous material handling and stowage procedures
ashore are provided in NAVSUP Pub 573.
Planning the Receiving Operation
Receipt operation ashore is more extensive than
afloat because of the large quantities and more variety
of materials being received. Planning and Coordinating
the tasks among the players responsible for different
phases of operation will facilitate receipt processing.
Using advance information before actually receiving
the material can make sure that necessary steps are
already taken to process them. For example, you can
use the advance shipment notice of a classified item to
ensure a qualified person is available to receive it. This
will enhance quick processing of material receipts.
Other documents that you can use for planning purposes
are
purchase orders,
contract schedules,
propositioned material receipt documents, and
advanced shipping documents.
The documents mentioned can give you the arrival
dates, category of material, and quantity of each item
category. This information should be provided to
personnel concerned with scheduling, storing,
transportation, packing, preservation, shipping, and
document processing. Storage personnel can use the
information to determine the location for the incoming
material. The dispatcher, on the other hand, can use the
information to ensure qualified operators are available
for the required MHE.
Planning and coordinating promote effective
storage space utilization, efficient assignment of
manpower and MHE, and recognition of items
requiring special handling.
During deployment, ships receive most stores by
underway replenishment (UNREP). While in port, the
bulk of material is delivered at pierside from the
supporting fleet and industrial supply center (FISC).
Senior AKs play an important role in an UNREP
evolution. You must work closely with other senior
petty officers and officers of the supply department.
You will be involved in planning the replenishment
procedures and in supervising the work in progress.
Your experience and knowledge are essential in
planning the UNREP evolution.
You should consider several factors in formulating
local plans for efficient functions of the UNREP under
local conditions. These factors include the cooperation
of various departments, the stations to be manned, the
amount of stores anticipated, the personnel and
equipment required, and the special procedures and
safety precautions normally employed during
replenishment operations.
When all necessary factors are considered and all
essential planning, teamwork, speed, and precision
have been executed skillfully, the UNREP operation
can then be termed successful.
It is important to remember that the ship is in a
vulnerable condition during an UNREP evolution.
Failure to take proper safety precautions because of
incomplete planning or confused execution could result
in a great loss of life and prevent the ship from
performing its primary mission.
Unloading Operations
Unloading operations require planning and on-site
supervision. Personnel performing this function must
be familiar with the procedures for inspection and
verification of material receipts. The mechanics of
unloading supplies vary according to the type of carrier,
type and weight of material, type of unloading facility,
and required MHE.
Personnel safety is important when unloading
supplies. Before unloading a sealed truck, check the
condition and number of the seal. If the seal is broken
or missing, annotate the discrepancy on the
documentation. In case of sensitive cargo, notify the
transportation office and security before unloading.
Conduct a preliminary inspection when the truck door
is opened. If there is evidence of damage or shortages,
suspend the unloading operation, if practical, pending
inspection by the carriers representative.
Unloading supplies at a receiving dock platform
requires abridge plate and dock leveler to permit entry
of MHE to the truck. Unloading at ground level
requires the use of a portable platform or ramp to allow
entry of the forklift truck.
Materials that need to be transported to the storage
area either directly from the carrier or receiving area
should be palletized. Maximum palletization facilitates
rapid and efficient unloading operations. Position
containers on the pallet in a way that the markings are
visible from the outer rows of the pallet load.
2-21
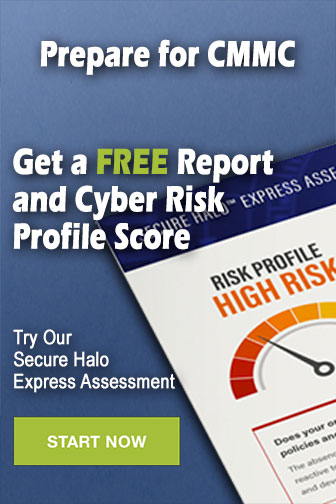