l
l
l
l
l
l
l
l
An aggressive security program is an effective
means of convincing personnel that they have
much more to lose than they do to gain by
engaging in theft.
The supervisor must set the proper example and
maintain a desirable moral climate for all storage
personnel.
Let storage personnel know that it is their
responsibility to report any loss to proper
authority.
Institute adequate inventory and control for
accounting material in storage.
Establish and monitor lock and key control
procedures.
Perform an investigation about suspected losses
quickly and efficiently.
Establish a material control system to include
inspection of delivery and vendor vehicles.
Establish accurate methods of taking physical
inventories and accounting of material
procurement, usage, and salvage,
Security of Items Requiring Special
Handling
Classified items should be kept separate from other
material. The most satisfactory method is to store these
items in a separate building with a higher degree of
physical protection. Where a separate building is not
available, a room, cage, or crib may be constructed
within a storage building. Spaces containing classified
material must be secured by means of an approved
locking system.
Pilferable and sensitive items should be stored in a
secured area to prevent theft. The storage area could be
a vault, cage, or fenced and locked security space.
Normally these items will not be stored with classified
material. However, when instances require these items
to be stored with classified material, the storage area
will be classified. In this case, the control applied to
these items is equivalent to the highest security
classification of any item in storage.
In some cases, pilferable items may require storage
in general-purpose spaces. For example, items were
received in large banded containers for which secure
storage space is not available. In this case, storage in a
general-purpose space is permitted. However, when
containers are opened to make issues, the residual
2-24
quantities should be transferred to the specified secured
area.
MATERIAL HANDLING
EQUIPMENT
Material handling is the process of moving material
to, from, and through one production area to the other.
The method used for moving material may vary but the
basic principles are the same. The following
information lists some of the guidelines in moving
material.
Keep handling of material to a minimum.
Minimum handling saves money and manhours
and reduces wear and tear of materials and
equipment.
Use standardized methods and equipment.
Standardization of equipment results in the
reduction of costs of operation, in maintenance,
repair, storage, and simplified issue procedures.
Select an MHE that can perform a multiple
number of applications. Consider flexibility
when selecting the type of equipment to be
used.
Minimize the use of specialized equipment.
Material handling operations requiring special
equipment are costly. The operating and
maintenance cost of special equipment is higher
than the cost for standard equipment.
Minimize the length and number of moves of
materials. Study the movement paths for
possibilities of reducing backtracking and
length of moves to facilitate better use of MHE
and personnel.
The rated capacity of an MHE must not be
exceeded. Overloading causes excessive wear
of equipment and creates additional accident
potential.
Greater payloads for each handling operation
result in less handling cost per piece.
The straight line flow of travel is the shortest
distance between production areas.
Preposition materials for MHE operations. This
means placing the material in the area that will
facilitate pickup and adhere to safety procedures.
For conveyor operations, place materials in such
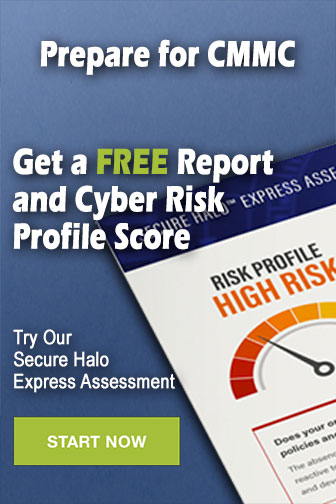