The S/LSC acts as the central point of entry for
processing issues off-line. It performs the same basic
functions as the supply response section (SRS) in
aviation stores division. The following sections describe
the responsibilities of the S/LSC for manual processing.
. The S/LSC or SRS checks the requisitions for
completeness and correctness of information.
. It is responsible for determining the avail ability
of the requested item by using the Master Stock Status
and Locator Listing (MSSLL). It writes the locations of
the material on the back of the form.
l It is responsible for putting the stock numbers
and locations of available substitute material on the back
of the form. For substitute issue, the S/LSC is
responsible for entering the stock number of material
identified for issue.
l When requested material is not available for
issue, the S/LSC forwards the requisition to the
procurement section for DTO processing.
l The S/LSC is responsible for pulling and placing
one copy of the issue documents in the issue pending
file (manual).
The next step in processing requisitions off-line is
the storeroom or warehouse. During this process,
personnel uses the marked-up requisition form to get the
material from the location. After finding the item,
storeroom personnel move it to the issue staging area
for pickup. See figure 7-6 for a sample of a complete
issue document processed off-line. The storeroom
personnel processes the issue document according to the
following transactions.
For complete issue, the following procedures apply:
Circle the quantity when issuing the full quantity
requested.
Signs and mark the staging area location on the
issue document.
Attach a copy of the issue document to the
material.
Deliver the issue document to the customer
contact point.
For standard pack adjustment, the following
procedures apply (fig. 7-7):
Adjust the issue quantity to match the standard
pack of the item; line out the requested quantity.
Enter and circle the issued quantity on the issue
document.
Mark the issue document with the words
STANDARD PACK ADJUSTMENT.
Sign the issue document and move material to
staging area. Mark the location of the staging
area on the issue document.
Attach a copy of the issue document to the
material.
Figure 7-6.-Complete issue (manual) documentation on DD Form 1348 (6-pt).
7-8
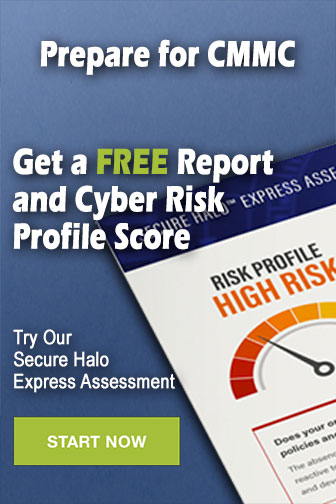