Block
13
14a
14b
15
Explanation
Funding and Accounting Data. For pack-
aging discrepancies, enter the accounting or
appropriation data required by the action
activity to credit the account of the reporting
activity for costs involved in correcting the
reported discrepancies. This item does not
apply to shipping discrepancies.
Typed or Printed Name, Title, and Phone
Number of Preparing Official. Self-
explanatory.
Signature. Self-explanatory.
Distribution Addressees for Copies. Enter
all other addressees that are to receive
copies of the report.
Use the Discrepancy in Shipment Report (DISREP)
for reporting transportation discrepancies in shipments.
These are shipments sent through the Defense
Transportation System (DTS) and shipments within
CONUS by commercial earner. Use the Standard Form
361 for submitting DISREP. NAVSUPINST 4610.33
(series) describes the types of discrepancies that need to
be reported on this form. Appendixes E and G of
NAVSUPINST 4610.33 provide detailed instructions
for preparing and distributing DISREP.
The primary purpose of reporting quality deficient
material is to provide feedback to responsible activities.
These are activities responsible for design,
development, purchasing, maintenance, and contract
administration. These activities use the report to
determine the cause of the deficiency, to correct them,
and to prevent recurrence.
The Ships Parts Control Center (SPCC) monitors
action started in response to quality deficient reports
(QDR). Also, the SPCC provides disposition
instructions to all activities concerned. Submit reports
for items with national stock numbers (NSN) to the
screening points, as specified in SECNAVINST 4855.6.
Send the original report for items with cognizance
symbols 1R, 4R, 4V, 4Z, 6R, W, and 7R to the cognizant
field activity (CFA). Send a copy of the report or the
original,
if
CFA
is
not
k n o w n , to
COMNAVAIRSYSCOM (AIR-51624). Send the report
to SPCC for material with a 9 in the first position of the
cognizance symbol.
You must identify and categorize quality deficient
material upon receipt or discovery. The originator
decides what product quality deficiency category to
assign. The following information is used for assigning
the category:
Category Definition
I
A product quality deficiency that may
cause death, injury, or severe
occupational illness. A deficiency that
would cause loss or major damage to a
weapons system. A deficiency that
directly restricts the combat readiness
capabilities of the using organization. A
deficiency that results in a production
line stoppage.
II
A product quality deficiency that does
not meet criteria stated in category I.
You should isolate defective material identified by
a QDR. Unless otherwise directed, hold the material as
an exhibit for a minimum of 90 days after submitting the
report to the screening point. Forward Category I QDR
within 1 day after receipt of the report. Forward
Category II QDR within 5 working days after receipt of
the report. The originating activity is responsible for
maintaining a log for assigning the control number and
to track replies to each QDR. The originator also
maintains copies of all QDR submitted for at least 2
years from the submission date of the QDR. The
originator is also responsible for responding to all
requests from screening action or support points
investigating the QDR. Refer to chapter 4 of NAVSUP
P-485 for sample copy of Standard Form 368.
DETERMINING WHEN A SHIPMENT IS
CONSIDERED COMPLETE
There are several factors that determine when
shipment is considered complete. The following texts
describe these factors.
Deliveries by Supply Officers Ashore
Deliveries by supply officers ashore to afloat
activities will be considered complete when stores are
turned over to the representative of the afloat activity.
Deliveries by Contractors
Deliveries by contractors to afloat activities will be
considered complete when stores were delivered to the
5-29
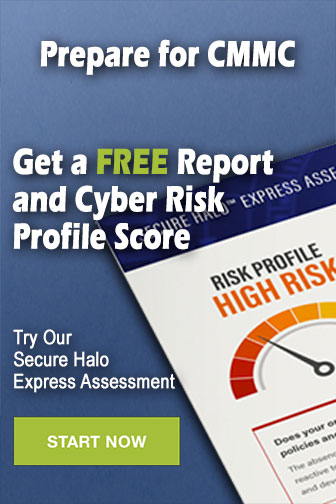