Fast Pay
The fast payment procedure allows payment, under
limited conditions, to a contractor before the
Governments verification that supplies were received
and accepted. Fast payment is for ordering supplies by
afloat and overseas activities only.
Fast pay is the payment made to a commercial
source based on proof of shipment by the vendor. This
means the vendor gets paid by submitting an invoice
proving that supplies were delivered to a post office,
common carrier, or Government receiving point. The
vendor agrees to replace, repair, or correct supplies not
received at destination, damaged in transit, or not
conforming to purchase agreements.
Use this method for buying material that does not
require technical certification at the destination. Prepare
DD Form 1155 according to enclosure 2, chapter 5, of
NAVSUPINST 4200.85 (series). The DD Form 1155
should include the fast payment procedure clause at
FAR 52.213-1 in full. Any BPA that may have fast
payment order should also contain the fast payment
procedure clause. Mark the original and all copies of the
DD Form 1155 with FAST PAY in bold letters. The
consignee must notify the purchasing office within the
following time frames:
. Receipt of conforming material within 10 days
from the receipt date
l Within 30 days if materials were not received by
the date shown in block 10 of DD Form 1155
l Within 10 days after receiving material that does
not conform to the requirements of the order
Indirect Delivery
When used for indirect delivery, blocks 13 and 14
of DD Form 1155 will show that the material and the
invoice will be delivered to a transshipper. In this case,
the supporting activity performs the technical inspection
and confirms acceptance of the material. The receiving
personnel need only verify the quantity of material
received. See figure 5-6 for a sample DD 1155
processed for indirect delivery.
The procedure for ordering material on a DD Form
1155 often involves a customer picking up the material.
This method is also known as bearer pick-up. We use
this method when the ordering department goes directly
to the vendor to get material. The supply officer
establishes local procedures to ensure proper receipt
processing. The procedures include requirements for
picking up all material and removing the DD Form 1155
copy from the bearer suspense file. The suspense copy
of DD form 1155 goes to the receiving section for
processing.
The ordering activity receives advance notice for
each DD Form 1155 purchase placed by another activity
in response to a requisition. The advance package
includes a copy of the DD Form 1155 and a
preaddressed card titled Report of Nonreceipt,
Damage, or Nonconformance.
Report of Receipt, Nonreceipt or
Nonconformance
The ordering activity completes and returns the
Report of Receipt, Nonreceipt, or Nonconformance
with an advance DD Form 1155. This form is used when
material received under contract on a DD Form 1155 is
not acceptable. The reasons for not accepting material
includes damaged in shipment or not technically
acceptable (direct shipments only). You also use this
form to report orders that were not received within 60
days of the specified delivery date. Receiving personnel
should then tell the procurement section to begin new
procurement action if necessary. When material has
been received on DD Form 1155, the Purchase Action
file copy will be certified as received. See figure 5-7 for
a sample Report of Receipt, Nonreceipt, or Non-
conformance.
DD FORM 250
The Material Inspection and Receiving Report, DD
Form 250, is used to verify material inspection and
acceptance for items received directly from a contractor.
The DD Form 250 may be used for shipments of
material procured by ashore activities on DD Form
1155. Receiving personnel will review the DD Form
250 to determine the type of certification required. The
following paragraphs explain the types of certification.
Acceptance At Destination (Code D)
Block 8 of DD Form 250 will show if acceptance at
destination (code D) was requested by the ordering
activity. If block 21B indicates procurement quality
assurance (PQA) and acceptance, you should contact a
qualified technician from the ordering department. The
technician will inspect and certify material acceptability
in block 21B.
The receiving personnel will certify the quantity
received in block 22. For quantity discrepancies, line out
the quantity in column 17, enter and circle the quantity
received. For material received in damaged condition,
5-9
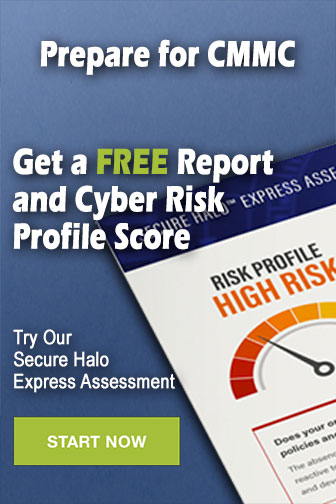