The first step is to remove the access covers and
fairings. To prevent the loss of these parts, they
should be left attached to the aircraft by one screw
or by a piece of safety wire.
The other screws
should be put in a container to prevent them from
being lost.
Disconnect bonding wires, electrical con-
nectors, and control linkage. Before disconnecting
cable linkage, you should relieve the tension at the
most convenient turnbuckle.
Next, support the
entire control surface, either manually or with
mechanical supports, in such a manner as to remove
all the load from the hinges. Remove the hinge
bolts by using a mallet and brass pin. The control
surface should be supported and all the hinges kept
in alignment until the last hinge bolt has been
removed.
On long controI surfaces, it may be
necessary to replace the hinge bolts with drift pins
to keep the hinges aligned while removing the
remaining hinge bolts.
Control surfaces are sometimes attached with
piano wire hinges. Removal of the piano wire can be
accomplished by removing the ends, securing one end
of the wire in the chuck of a hand drill, and rotating
the wire with the drill while withdrawing it.
Excessive spinning will have a wearing effect on the
hinge material and should be avoided. The reuse of
piano hinge wire is not safe; therefore, any wire
removed should be discarded.
After all the hinges are disconnected, remove
the control surface from the aircraft and support it
carefully to prevent damage to the hinge brackets
and adjoining surfaces.
the hinges to prevent
damaged.
Before installing a
Replace the hinge bolts in
them from being lost or
control surface, check the
identification tag to determine its proper location on
the aircraft. Place the surface in position carefully.
You should ensure that all the hinge holes are properly
aligned. Drift pins may be used to align the holes.
With the control surface correctly supported, install
the hinge bolts. For a surface attached by piano hinge
wire, a new wire should be used. After a control
surface is installed, connect the control linkage and
check the rigging of the system.
Some flight control surfaces are balanced at the
time of manufacture by adding counterweights to the
inside of the leading edge of the control surface. This
balance must be maintained (within certain
tolerances) throughout the service life of the control
surface because flutter or dynamic oscillation of these
surfaces in flight is not desirable. Balance tolerances
are always specified in the aircraft structural repair
manual.
Alignment of the airframe structure means
checking the position relationship of each major
componentthe wing group, tail group, and
fuselage group-to the other. The alignment of the
airframe is important since it is directly related to
the aerodynamic performance of the aircraft.
Misalignment may affect the flight characteristics of
the aircraft, and consequently, the efficiency of the
pilot-aircraft combination.
For this reason and for purposes of determining if
any hidden structural failures exist, an alignment
check should be performed when an aircraft has
encountered excessive gs in flight, when a hard
landing has been experienced, or when the aircraft has
been subjected to extensive damage.
The need for an alignment check after extensive
damage is rather apparent; however, this is not
necessarily so in situations where the aircraft exceeds
the g design limit or where a hard landing has been
experienced. The alignment check under these
conditions may expose damage that might otherwise
go unnoticed.
ALIGNMENT LEVELING METHODS
Prior to making an alignment check, it is
necessary to level the aircraft both laterally and
longitudinally. This may be accomplished by using
the transit, spirit level, or plumb bob and datum plate
method. You should always use the method of
leveling specified by the manufacturer.
When you are leveling an aircraft for an
alignment check, the aircraft should be inside a
hangar where air currents will not interfere with the
accuracy of the alignment readings. Jacks should be
used to control the attitude of the aircraft during the
check.
9-53
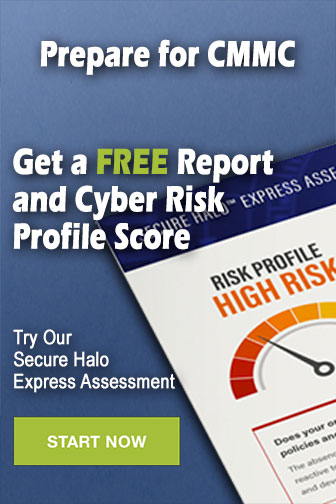