The wingtip brake consists of a set of trailing
edge surfaces for each wing. The lower half attaches
to the wing structure with two external fixed hinges.
The upper half is attached to the wing at the same
wing station with two adjustable tension lengths. An
interconnecting hinge between the upper and lower
halves provides a common connection point for the
actuating cylinders. The hinge provides symmetrical
deflection of upper and lower panels. Each panel can
open up to 60 degrees for a total angle of 120 degrees
for each wingtip brake. When retracted, they lie flush
with the wing surface. They can extend and hold at
any angle between 0 and 60 degrees, depending upon
the amount of aerodynamic braking desired.
A mode selector switch permits simultaneous or
independent operation of the wingtip and fuselage
speed brakes, with the speed brake control switch
located on the right throttle quadrant power lever.
Moving the SPD BRK switch to the forward position
closes the brakes. Moving it to center position holds
the brakes at any desired angle. Moving it aft opens
the brakes. The switch is spring-loaded to neutral
from the aft position only.
Selecting the open position energizes the selector
valve, porting hydraulic pressure from the combined
hydraulic system to the extended side of the actuating
cylinder. When the switch is positioned to closed, the
opposite solenoid energizes. Pressure is ported to the
retract side of the actuating cylinders. With the
switch in neutral, hydraulic fluid is blocked from both
the extend and retract sides of the speed brake
cylinders. This action hydraulically locks the speed
brakes. If the electrical circuit fails, the selector valve
is de-energized as a fail-safe feature and the speed
brakes retracts.
The wingtip speed brake control system normally
depends upon the hydraulic flow regulators to
maintain symmetrical extension of the left and right
brakes.
If a malfunction causes asymmetry of
extension, an electrical disparity signal is sensed by
the speed brake null detector. When the disparity
between the extension of the left and right brake
reaches 8 degrees, the null detector de-energizes the
selector valves and causes the speed brakes to close.
On some aircraft, the synchronization mechanism
(fig. 9-41) consists basically of synchronizing
linkage, two torsional bungee assemblies, and a cable
run interconnecting the three mechanisms to a
mechanical synchronizing control valve. The
synchronizing mechanism is a comparative linkage
type that senses unequal motion between the two
brake surfaces. Movement of either speed brake
transmits through the torsional bungee assembly and
the cables to the synchronizing mechanism. Any
unequal movement upsets the synchronizing
mechanisms neutral position, displacing the
synchronizing valve shuttle. When the speed brakes
are opening or closing, the valve is normally in
neutral as long as the travel of both sides is equal.
When unequal travel moves the valve shuttle out of
neutral, the valve will relieve hydraulic pressure from
the speed brake actuating cylinder, producing the
hugest opening angle. This decelerates the opening
of the speed brake or bleeds down the speed brake
with the largest angle until the disparity is within
limits and the shuttle returns to neutral. On later
models this mechanical synchronization system has
been deleted.
If the mechanical synchronization system fails to
maintain synchronization within 8 degrees, the
electrical fail-safe system operates and de-energizes
the selector valve to close the speed brakes. If the
synchronizing linkage becomes jammed, the torsional
bungee assembly can be forced out of detent, isolating
the linkage from the speed brake and preventing
damage to the linkage because of overloads.
The bungee in the synchronizing mechanism
linkage acts as a rigid length to the synchronizing
valve during normal operation of the wingtip speed
brake. If the valve becomes jammed, abnormal loads
on the bungee will cause it to give and relieve the
excessive loads before damage to the valve, linkage,
or bungee occurs.
TRIM SYSTEM
A trim system is provided in the flight controls to
lessen the need for constant effort on the part of the
pilot to maintain the desired heading and altitude.
The trim system stabilizes the aircraft during flight.
Lateral Trim
The aileron trim control system is shown in
figure 9-42. The illustration represents a trim tab
arrangement similar to that found on aircraft equipped
with conventional aileron systems.
Operation of the lateral and longitudinal trim
systems is usually controlled by a five-position,
four-throw, momentary ON contact switch with a
center OFF position.
The switch is found on the
control stick grip. This switch electrically energizes
the trim control motor, which operates the trim
9-48
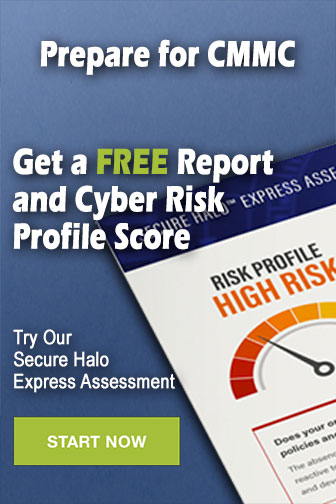