inputs. This modification causes the eight spoiler
actuators to position their spoilers 3 degrees up from
the 0-degree position.
The pitch computer also
generates the DLC servo actuator command drive at
the time of DLC engagement. This command drive,
which is applied to the DLC servo actuator, drives the
stabilizers to the 6-degree trailing edge down position
from the 0-degree position. In DLC, the pitch
computer and the roll computer permit additional
spoiler and stabilizer control through the
DLC-maneuver, flap-glove vane thumb wheel control
on the control stick grip.
Rotating the thumb wheel fully forward, through
modified spoiler and DLC command drives, extends
the spoilers to the 12-degree position. The stabilizer
is driven to the 8-degree trailing edge down position.
Rotating the thumb wheel control fully aft retracts the
spoilers to the 4.5-degree position and drives the
stabilizers to 0 degrees. This maintains aircraft
attitude while changing the vertical descent rate.
Direct lift control can be disengaged by momentarily
pressing the DLC engage-chaff dispense push-button
switch or by setting either throttle lever to
power.
WING SURFACE CONTROL SYSTEM
military
The wing surface control system controls the
variable geometry wings to increase aircraft
performance at all speeds and altitudes. The system
also provides high lift and drag forces for takeoff and
landing. It provides increased lift for maneuvering,
and at supersonic speeds, aerodynamic lift to reduce
trim drag.
The wing sweep control initiated at the throttle
quadrant provides electronic or mechanical control of
a hydromechanical system that sweeps the wings.
See figure 9-38. The wings sweeps from 20 degrees
through 68 degrees in flight. On the ground, a wing
sweep position of 75 degrees is available (through
mechanical control) for spotting the aircraft or
enabling a wing sweep control self-test. See
figure 9-39.
Electronic Control
A wing sweep under electronic control is initiated
at the throttle quadrant.
Four modes are
availableautomatic, aft manual, forward manual, or
bomb manual. Selection of these modes causes the
air data computer to generate wing sweep commands
consistent with the aircraft speed, altitude, and
configuration of the flaps and slats. The commands
are applied through the wing-flap glove-vane
controller to the wing sweep control drive servo.
They are converted to mechanical rotary force. This
force, transferred to the wing sweep/flap and slat
control box, causes the wing sweep hydraulic control
valve to operate hydraulic motors that are driven by
the flight and combined hydraulic power systems to
sweep the wings. The flight hydraulic power system
positions the right wing, and the combined hydraulic
power system positions the left wing. A
synchronizing shaft (fig. 9-38) interconnects the
wings to ensure symmetrical operation. If a hydraulic
system fails, it provides the driving force for
sweeping the wing affected by the failed system.
Wing sweep commands generated by the air data
computer are limited by the configuration of the
auxiliary flaps, maneuver flaps, and slats. With the
auxiliary flaps extended, wing sweep is limited to
21.25 degrees. The maneuver flaps, with or without
slats extension, limit wing sweep to 50 degrees. To
prevent structural damage to the wings during
negative-g conditions, wing sweep is interrupted to
prevent wing sweep changes until the negative-g
condition no longer exists. In the automatic mode, the
wings are positioned at a rate of 7 degrees per second.
Figure 9-39.Wing oversweep Positionmanual control.
9-45
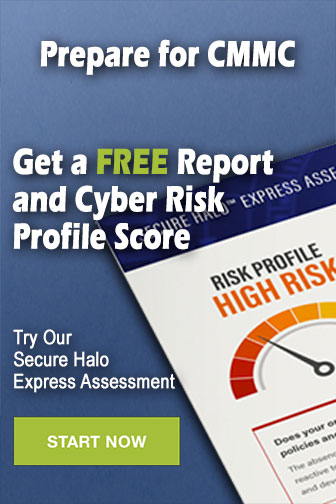