the terminal from right to left. The dies compress the
terminal barrel onto the cable, and swaging occurs.
Rotation of the dies is accomplished by opening and
closing the handles.
After completion of swaging and removal of the
fitting from the swaging tool, measure the outside
diameter of the shank with a micrometer or with the
gauge furnished with the swaging outfit to determine
whether or not the terminal has been swaged
sufficiently. This may be determined by checking the
measurement with the applicable cable terminal table
in NAVAIR 01-1A-8.
The pneumatic swaging tool shown in figure 9-29
is a lightweight portable unit designed to precision
swage the metal of a terminal into the interstices
(crevices) of the cable strands. The swager may be
mounted on a baseplate and used on a bench, or it can
be taken to the job. When the swaging tool is taken to
the location of the job, it may be held in your hand or
cradled in your arm.
The pneumatic swaging kit has several different
sizes and types of dies used for swaging ball-and-
sleeve terminals and for cutting and trimming cable.
Like the mechanical swaging tool, the dies come in
matched sets and must be used together. The dies are
installed by inserting either die through the yoke
opening into the die cavity. The keyway should be
down and the shank facing the rear of the swager.
Slide the first die back in order to clear the opening
for the insertion of the mating die. The second die is
inserted with the shank facing forward.
The following step-by-step procedures are
recommended for setting up the pneumatic swaging
tool :
1. Connect the air supply to the foot valve. For
efficient operation, use an inlet air line with at least
3/8-inch inside diameter and a minimum of 90 pounds
of line pressure.
2. Connect the swager air line to the foot valve.
3. Clean the dies, remove any steel particles that
may have adhered to the die cavity, and apply a light
film of oil to the entire die.
4. Insert the dies in the swaging tool as
previously described.
WARNING
Do not insert or remove dies until the air
supply that is connected to the swager is
shut off. Failure to secure the air supply
connected to the swager could result in
personal injury to the operator.
With the pneumatic tool set up for use, perform
the following steps while swaging terminals to cables:
1. Position the terminal on the cable, using the
old cable as a pattern, or follow the instructions given
in the applicable technical directives. When you are
using a ball terminal, a minimum of 1 1/2 inches of
cable must extend beyond the ball to allow room for
holding and turning the terminal during swaging. The
excess is trimmed, if necessary, after the swaging
operation. When you use MS 20667 terminals,
1/4 inch of cable must extend through the terminal.
On all other terminals, the cable is bottomed (inserted
all of the way into the terminal).
2. Each terminal is cleaned with a suitable
solvent, and then coated with a light oil.
3. With the terminals positioned in the cavity of
the forward die, slide the rear die to its forward
position using the slot provided in the yoke for the
index finger.
NOTE: To prevent damage to terminal or
cable during the swaging cycle, maintain light
pressure on the cable towards the front of the
swager. This holds the terminal and cable
firmly in the forward die cavity.
4. Depress the foot valve firmly and rotate the
cable back and forth in 180-degree arcs or complete
revolutions. The length of time the foot valve is held
depends upon the type and size of fitting being
swaged. The proper time can be found by referring to
the chart supplied with the pneumatic swaging tool.
If the terminal will not rotate, stop swaging
immediately; rotate the terminal 90 degrees, and start
swaging again.
5. Release the foot pedal to stop swaging, and
remove the terminal from the swaging tool for
inspection. If the diameter is oversize or the terminal
surface is too rough, repeat the operation.
If swaged terminals are to be used on both ends of
the cable, recheck the overall length of the cable and
trim it, if necessary, prior to installing the second
terminal. Make certain that all additional fittings and
accessories, such as cable stops and fairleads, are
slipped onto the cable in the proper sequence. The
other terminal may then be swaged, using the same
procedures as used for the first one.
Proof-Testing Cables
All newly fabricated cables should be tested for
proper strength before they are installed in aircraft
The test consists of applying a specified tension load
on the cable for a specified number of minutes. The
9-36
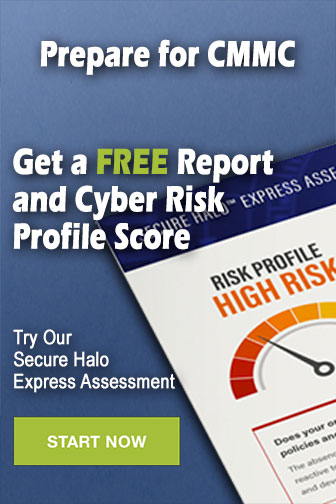