cables, use the end of the cutting blade, and cut only a
few strands at a time.
The most satisfactory method of cutting cables is
with a cable-cutting machine that has special jaws to
accommodate various sizes of cable. See figure 9-28.
To use this machine, position the cable in the proper
diameter groove and hold the cable firmly within
2 inches of the cutting blades. Hold the cable at right
angles to the cutting blades and pull the operating
handle down sharply.
A cold chisel and a soft metal block may also be
used for cutting cables. This method should be used
only as a last resort because of the way the cable ends
will be frayed.
Terminal Swaging
After the cable is cut, the next step in making up an
aircraft cable is attachment of the terminals.
Most
terminal fittings are SWAGED onto the ends of control
system cables. Swaging is essentially a squeezing
process in which the cable is inserted into the barrel of
the terminal. Then pressure is applied by dies in a
swaging machine to compress the barrel of the terminal
tightly around the cable. The metal of the inside walls
of the barrel is molded and cold flowed by force into the
crevices of the cable. Figure 9-29 shows two types of
hand-swaging tools. The one in the upper part of the
illustration is mechanically operated, while the lower
one is pneumatically operated.
When you prepare to swage a terminal, cut the
cable to the required length. Be sure to allow for the
elongation (increase in length due to stretching) of the
fitting that will occur during the swaging process.
The amount of elongation will vary with the type and
size of fitting used. Therefore, the elongation must be
taken into account whenever you make up any cable.
The Structural Hardware Manual, NAVAIR 01-1A-8,
provides elongation data for all types and sizes of
fittings.
Make sure that the cable end is cut square and
clean and that all strands remain in a compact group,
as shown in figure 9-30. Place a drop or two of light
lubricating oil on the cable end. Then, insert the end
into the terminal to a depth of about 1 inch. Bend the
cable toward the terminal, straighten it back to the
normal position, and then push the cable all the way
into the terminal barrel. This bending process puts a
kink in the cable end to hold the terminal in place until
the swaging operation is completed. It also tends to
separate and spread the strands inside the terminal
barrel and reduces the strain caused by swaging.
Both of the hand-swaging tools shown in
figure 9-29 are widely used by naval aircraft
maintenance activities. The procedure for using both
types is described in the following paragraphs.
Figure 9-28.Cable-cutting machine.
9-34
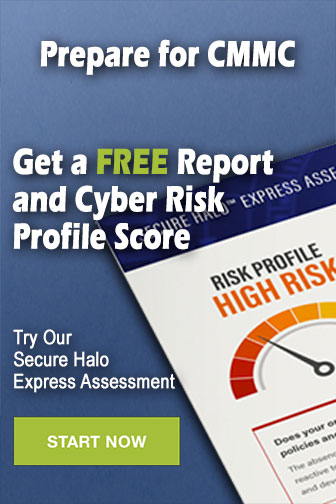