the outer cylinder. Carefully withdraw the inner cylinder
from the outer cylinder. Pull the metering pin and
bulkhead from the inner cylinder with a smooth
controlled force. Tag or keep parts together to expedite
reassembly.
Cleaning
Thoroughly clean all parts of the recoil strut
assembly, using P-D-680 dry-cleaning solvent (spray or
dip) or a similar cleaning solvent. Dry thoroughly with
clean, dry, compressed air, paying particular attention
to all recesses and internal passages. Use the cleaning
solvent in a well-ventilated area. Avoid prolonged
inhalation of fumes. Keep solvent away from open
flames.
Cleaned parts that normally come in contact with
fluid during operation of the strut should be coated with
hydraulic fluid. Depending on local conditions, it may
be desirable to also coat external highly machined
surfaces.
Wipe the lower bearing clean with a clean, lint-free
cloth dampened with hydraulic fluid. Do not touch
machined surfaces with your bare hands. Do not use
compressed air to dry bearings. Clean the bearings with
new cleaning solvent and dry with a lint-free cloth.
Inspection
Perform a thorough visual inspection of the
disassembled parts for serviceability. Packing grooves
and surrounding areas should be inspected for scratches,
burrs, nicks, or other roughness that might cut packings
on installation or cause seal failure during strut
operation. Inspect machined surfaces for mars,
abrasions, gouges, grooves, scores, scratches, and
corrosion. If any parts are suspected of having cracks,
the part should be inspected using one of the
nondestructive methods of testing.
Check all threaded parts for distorted or mutilated
threads. Inspect plated surfaces for blistering, flaking,
wear, or other defects.
Within the limits of practicability, check all holes
for concentricity and taper, using an internal
micrometer, hole gauges, plug gauges, or similar
equipment. Check the angle between the piston and the
axle. Check to ensure that the brake flange is
perpendicular to the axle. Inspect all ports, bores, and
passages for cleanliness. Place bearings next to a
sensitive compass to check for residual magnetism.
Bearings should be inspected for obvious damage,
Brinelling (shallow indentations in the raceway), or
corrosion. Rotate bearing races and check for
roughness, binding, or looseness. Bearing retainers must
be checked for cracks, warpage, and corrosion. Refer to
the tables furnished in the applicable accessories manual
or the Intermediate Maintenance Section of the
appropriate MIM for service limits established for
critical areas.
Repair or Replacement
Repair or replace all parts that show evidence of
excessive wear, scoring, or corrosion. Replace all parts
that show wear beyond the dimensions specified in the
inspection standards tables found in most 03 manuals or
MIMs.
Each time the strut is disassembled, all preformed
and special packings should be replaced, although they
may appear to be serviceable.
NOTE: Never work on machined services with
metallic tools. Always use brass O-ring tools for
checking scratches and removing or replacing
seals and gaskets.
Blend out minor scratches, nicks, and burrs from
machined surfaces of steel parts with a crocus cloth. Use
aluminum oxide abrasive cloth to polish aluminum
parts. The smoothness of the repaired area must be equal
to or smoother than the finish of the surrounding area.
Do not attempt to remove normal wear marks from the
sliding surface of the piston.
NOTE: Partial removal of plating from the
inner cylinder will condemn the part from
further service, pending replating of the
cylinder. Portable brush-type plating equipment
is available in some intermediate maintenance
activities for touch-up plating of minor areas.
Areas with damaged paint or other protective
finishes must be restored to a serviceable condition.
If any bushings require replacement, the mating
bushing must also be replaced.
Reassembly
Reassemble the strut assembly in essentially the
reverse order of disassembly. Exercise adequate
precautions to ensure that dirt, dust, grit, or other foreign
12-27
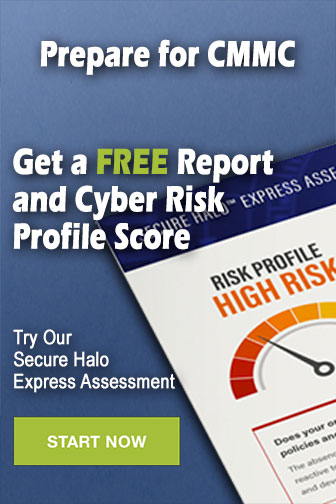