Figure 12-24.-Gladden master brake cylinder.
When the pedal pressure is released, the springs
return the valve and the piston to their neutral position.
The retracting brake assembly piston forces the return
fluid back through the piston orifice to the brake
reservoir.
Figure 12-25.--Power boost brake system.
POWER BOOST BRAKE SYSTEM
As a general rule, the power boost brake system is
used on aircraft that land too fast to use the
independent-type system, but are too light in weight to
require the power brake control system. In this type of
system, a line is tapped off from the main hydraulic
system pressure line, but main hydraulic system
pressure does not enter the brakes. Main system pressure
is used only to assist pedal movement. This is
accomplished through the use of power boost master
cylinders.
A schematic diagram of a typical power boost brake
system is shown in figure 12-25. The normal system
consists of a reservoir, two power boost master
cylinders, two shuttle valves, and the brake assembly in
each main landing wheel. A compressed air bottle with
a gauge and release valve is installed for emergency
operation of the brakes.
In this system (fig. 12-25), main hydraulic system
pressure is routed from the pressure manifold to the
power boost master cylinders. When the brake pedals
are depressed, fluid for actuating the brakes is routed
from the power boost master cylinders through shuttle
valves to the brakes.
12-31
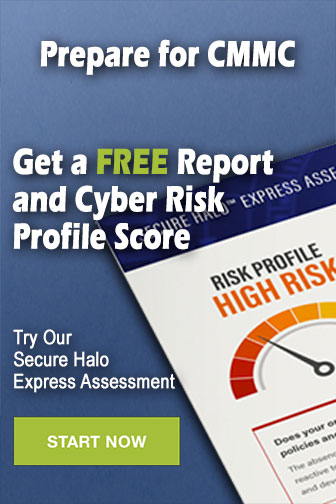