Figure 2-30.Structural screws.
slotted or recessed for the various types of
screwdrivers. See figure 2-30.
MACHINE SCREWS.The commonly used
machine screws are the flush-head, round-head,
fillister-head, socket-head, pan-head and truss-head types.
Flush-Head.Flush-head machine screws are
used in countersunk holes where a flush finish is
desired. These screws are available in 82 and 100
degrees of head angle, and have various types of
recesses and slots for driving.
Round-Head.Round-head machine screws are
frequently used in assembling highly stressed aircraft
components.
Fillister-Head.Fillister-head machine screws
are used as general-purpose screws. They may also
be used as cap screws in light applications such as the
attachment of cast aluminum gearbox cover plates.
Socket-Head.Socket-head machine screws are
designed to be screwed into tapped holes by internal
wrenching. They are used in applications that require
high-strength precision products, compactness of the
assembled parts, or sinking of the head into holes.
Pan- and Truss-Head.Pan-head and truss-
head screws are general-purpose screws used where
head height is unimportant. These screws are
available with cross-recessed heads only.
SELF-TAPPING SCREWS.A self-tapping
screw is one that cuts its own internal threads as it is
turned into the hole. Self-tapping screws can be used
only in comparatively soft metals and materials.
Self-tapping screws may be further divided into two
classes or groups: machine self-tapping screws and
sheet metal self-tapping screws.
Machine self-tapping screws are usually used for
attaching removable parts, such as nameplates, to
castings. The threads of the screw cut mating threads
in the casting after the hole has been predrilled. Sheet
metal self-tapping screws are used for such purposes
as temporarily attaching sheet metal in place for
riveting. They may also be used for permanent
assembly of nonstructural parts, where it is necessary
to insert screws in blind applications.
CAUTION
Self-tapping screws should never be used to
replace standard screws, nuts, or rivets in
the original structure. Over a period of
time, vibration and stress will loosen this
type of fastener, causing it to lose its
holding ability.
WASHERS
Washers such as ball socket and seat washers,
taper pin washers, and washers for internal-
wrenching nuts and bolts have been designed for
special applications. See figure 2-31.
Ball socket and seat washers are used where a bolt
is installed at an angle to the surface, or where perfect
alignment with the surface is required at all times.
These washers are used together.
Taper pin washers are used in conjunction with
threaded taper pins. They are installed under the nut
to effect adjustment where a plain washer would
distort.
Washers for internal-wrenching nuts and bolts are
used in conjunction with NAS internal-wrenching
bolts. The washer used under the head is countersunk
to seat the bolt head or shank radius. A plain washer
is used under the nut.
2-22
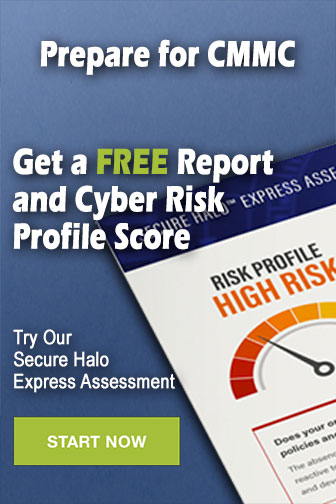