result in severe injury or death to personnel and
damage to or destruction of aircraft. Therefore,
due to the inherent dangers associated with
ejection seats and canopy systems, a seat/canopy
check-out procedure is required. The Egress/
Environmental Work Center (AME shop) is re-
sponsible for indoctrinating all personnel in the
hazards and safety precautions associated with
these systems. A thorough seat check-out will be
given, by a qualified Aviation Structural Mechanic
(Safety Equipmentman) (AME), to all newly
assigned maintenance personnel prior to their
performing any aircraft maintenance work on the
aircraft, and every 6 months thereafter. In
addition, any personnel removed from aircraft
maintenance responsibilities for over 90 days must
receive a seat check-out before performing any
aircraft maintenance. The AME work center and
the other maintenance work centers will maintain
records of seat check-outs, including date given,
date due, and the signature of the AME
performing the check-out.
The seat check-out program will be established
by a squadron MI. All personnel due seat check-
out requalification will be listed in the monthly
maintenance plan.
EJECTION SEAT CARTRIDGES
AND CARTRIDGE-ACTUATED
DEVICES (CAD)
The types of explosive devices incorporated
in egress systems are varied. The AME working
with these devices must know how they function,
their characteristics, how to identify them, their
service-life limitations, and all safety precautions.
The AME who understands the importance of
all these factors and who correctly uses the
maintenance manuals is better equipped to
supervise and train others. The following manuals
are required for the AME to meet the above
requirements:
1. Description,
Preparation for use, and
Handling Instructions, Aircrew Escape
Propulsion System (AEPS) Devices, NAVAIR
11-85-1
2. General Use Cartridges and Cartridge
Actuated Devices for Aircraft and Associated
Equipment (CADS), NAVAIR 11-100-1.1,
NAVAIR 11-100-1.2, NAVAIR 11-100-1.3
3. Specific aircraft MIMs
4. OP 4, Ammunition Afloat
5. OP 5, Ammunition and Explosives Ashore
Service Life
The service life of a CAD is the specific period
of time that it is allowed to be used. These periods
of time are affected by various environmental
conditions, which have resulted in the assignment
of time limits or overage requirements. These
limits are shelf life and installed life.
The establishment of service-life limits is based
upon design verification tests, qualification tests,
and surveillance evaluations. The established
limits are approved by the Naval Air Systems
Command. Therefore, the establishment of
service-life time limits is not arbitrary and must
be adhered to as specified.
Before deployment to areas that do not permit
ready supply and servicing of cartridges or
cartridge-actuated devices, an inspection must be
made of all CAD service-life expiration dates. If,
during this inspection, it is determined that a CAD
will become overage during the period of the
deployment, the CAD must be replaced prior to
the deployment. Before installation of any CAD,
the service life expiration date of the unit must
be checked to ensure that the unit is not overage
and will not become overage prior to the next
periodic maintenance cycle of the aircraft.
During standard depot-level maintenance
(SDLM), the expiration dates of all installed
CADs must be checked. Those CADs assigned to
organizational level for maintenance and have
expiration dates prior to the next scheduled
inspection after the aircraft is returned to its
custodian must be replaced. CADs assigned to
depot level for maintenance that have expiration
dates falling prior to the next scheduled SDLM
should also be replaced. The exception is systems
replaced exclusively through the use of a field
modification team. Adherence to these procedures
will prevent loss of aircraft mission capability due
to CAD service-life expiration.
Expiration Dates
To determine service-life expiration dates,
both the shelf life and installed life must be
computed. First, compute the shelf life of the
CAD by using its lot number to determine the
month and year of manufacture. Refer to table
1-1 to ensure correct interpretation of the lot
number since there are currently two methods
used to derive lot numbers. Obtain the established
shelf life (number of months and years) for the
individual CAD from the NAVAIR 11-100-1
series manual. Add this figure (shelf life) to the
1-8
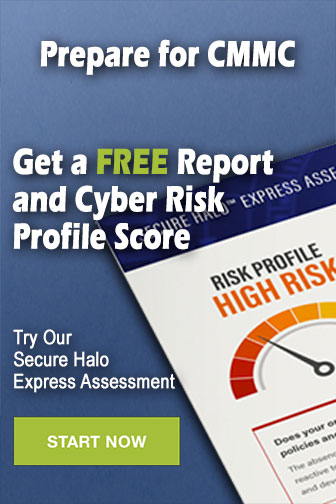