to vent both transfer cylinders and the unlock
port of the canopy-lock pneumatic actuator
overboard. The weight of the canopy closes it;
pneumatic power is not required. The closing
time, approximately 10 seconds from the fully
open position, is controlled by the flow regulators
in the open and close control modules of the
hydraulic actuator. The final closing motion of
the canopy actuates the pneumatic timer to direct
325-psi nitrogen from valve No. 2 of the control
module to the lock port of the canopy-lock
pneumatic actuator, unlatching the ball locks. The
actuator piston retracts and, by reverse action,
moves the canopy forward to engage the canopy
hooks in the sill locks. With the canopy in its full
forward positions, the lock lockpin engages and
prevents aft movement of the canopy. The final
motion of the lock lockpin opens the canopy
switch, breaks the circuit to the canopy caution
indicator light on the caution advisory indicators,
and the lights go off.
Boost Closing Mode
To close the canopy under high headwind
conditions, the canopy control handle must be
moved to BOOST. On aircraft not modified by
AFC 95, the control handle must be rotated out-
board to move the handle pasta stop to BOOST.
Valve No. 4 in the control module is positioned
to direct 790-psi nitrogen through the C2 port of
the canopy hydraulic actuators to the close
transfer cylinder. This nitrogen, acting against the
transfer cylinder piston, causes the hydraulic fluid
on the opposite side of the piston to retract the
actuator. The other valves in the control module
are positioned the same as when CLOSE is
selected, and the system functions in the
same manner to lock the closed canopy.
The closing time for this mode of operation is
also controlled by the flow regulators in the
open and close control modules of the hydraulic
actuator.
Auxiliary Opening Mode
The auxiliary opening mode is used to unlock
the canopy when normal pneumatic system
reservoir pressure drops below 225 psi. To
prevent further depletion of nitrogen pressure in
the normal system, a low-pressure sensor
repositions valves No. 5 and No. 6 in the control
module. The canopy must now be unlocked by
activating the auxiliary opening mode. To set the
canopy control handle to AUX OPEN on aircraft
not modified by AFC 95, the handle must be
rotated outboard to move past a stop (the
handle will remain in the AUX OPEN position).
When the control handle is set to AUX OPEN,
the auxiliary unlock pneumatic release valve
releases pressurized nitrogen from the auxiliary
pneumatic reservoir. Nitrogen pressure from this
reservoir flows through a 325-psi pressure reducer,
through the release valve and pneumatic unlock
shuttle valve, to shift position of the shuttle valve
internal spool. This directs nitrogen pressure to
the unlock port of the canopy-lock pneumatic
actuator, unlocking the canopy. Valve No, 1 in
the control module directs reservoir pressure to
the open transfer cylinder of the canopy hydraulic
actuator. This low-pressure nitrogen, acting
against the transfer cylinder piston, counter-
balances the weight of the canopy. The canopy
can then be easily opened and closed manually.
The canopy cannot be locked closed under these
conditions. To return the system to normal
operation, the control handle must be set to
OPEN and, on aircraft not modified by AFC 95,
rotated outboard to move past a stop. The release
valve eccentric cam must be manually reset to
block auxiliary nitrogen pressure flow to the
shuttle valve and to vent the pressure in the
canopy-lock pneumatic actuator.
SYSTEM COMPONENTS
The purpose of each of the major components
of the F- 14 clamshell canopy system is presented
in the following paragraphs. Refer to figure 2-2
to see how each component fits into the overall
system.
Canopy Hydraulic Actuator
The canopy hydraulic actuator opens and
closes the canopy. It consists of a double-acting
hydraulic cylinder, two transfer cylinders, and two
hydraulic control modules. The transfer cylinders
convert pneumatic pressure from the canopy
pneumatic control module to hydraulic power.
The hydraulic control modules contain
pneumatically actuated shutoff valves that
2-3
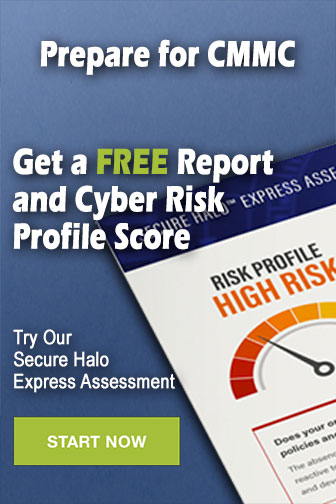