performs the primary sensing function, and the
other is used for the built-in test (BIT).
Fairing Interlock Switch
The fairing interlock switch provides an
electrical connection for the missile coolant pump
motor and pressure switch circuits. The switch is
closed when the right Phoenix fairing is installed.
Liquid Cooling Control Panel
The liquid cooling control panel is located on
the NFOs left side console. When the liquid cool-
ing switch is set to the AWG-9/AIM-54 position,
it activates both the radar and missile cooling
loops of the system.
MAINTENANCE SAFETY
PRECAUTIONS
The Phoenix missile requires a completely
contaminant-free cooling system. Keeping the
system clean requires the use of toxic fluids
that must be used with special care. It is
important to handle this system with the same
care as you would handle an oxygen system.
The following information is of special interest
and should be kept in mind when working on this
system.
1. If more than 1 gallon of coolant is required
to fill the expansion tank, you should flush and
refill the system, using the liquid coolant service
unit (LCSU) shown in figure 1-19. For detailed
LCSU operating procedures, you should refer to
the applicable MIM.
2. The cooling system should only be serviced
with Flo-cool 180, Coolanol 25, or Coolanol 25-R.
If you use another type of coolant, you may
damage the missile components. It is a require-
ment that you wear a respirator or work in an area
with forced ventilation while working with these
coolants. Additionally, you must wear chemical
splashproof goggles and gloves.
3. When you use trichlorotrifluoroethane,
MIL-C-81302, Type I or II, to clean fittings and
hoses, exercise extreme caution. You must wear
a respirator and chemical splashproof goggles and
gloves. The task should be performed in an area
with forced ventilation. Smoking is prohibited in
the area where this chemical is being handled.
Keep the trichlorotrifluoroethane from coming in
contact with your skin, eyes, and clothes. Do not
breathe the toxic vapors.
4. To prevent contamination of the tem-
perature control system and possible damage to
its componenets, absolute cleanliness of your
equipment, work area, and coolant must be main-
tained. You should ensure that dust caps, flushing
jumpers, hoses, and bleed lines are thoroughly
cleaned with trichlorotrifluoroethane and a lint-
free cloth. The cleaned components should be air-
dried before installation. Do not allow O-ring
seals to soak in cleaning fluid before or after
cleaning because this will cause hardening of the
O-rings and. premature failure.
5. When adding coolant with the fluid
makeup unit (fig. 1-20), add the coolant slowly.
Rapid pumping may cause the pressure relief
valves on the makeup unit and in the aircraft to
open.
6. Coolant spilled on the aircraft can
damage the paint. Spillage should be wiped up
immediately. Spillage on a coaxial cable may
cause the cable to come apart.
7. To take a coolant sample, the coolant must
have been circulated for at least 5 minutes by the
aircraft, powered pump. This circulation ensures
that the sample will be representative of coolant
in the entire system. The sample should be taken
from the AIM-54 supply bleed port.
Figure 1-20.Liquid coolant fluid makeup unit.
l-27
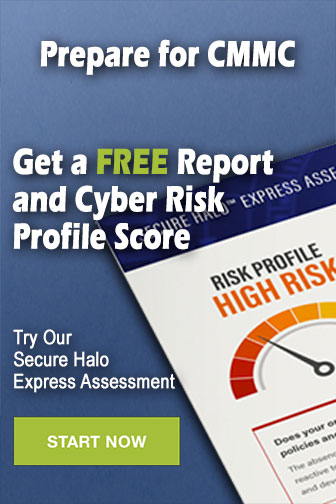