with steel taps or hobnails. Oxygen-permeated
clothing will burn vigorouslya most painful way
to die.
11. When servicing a liquid oxygen system,
ensure that only oxygen conforming to specifica-
tion MIL-0-27210D is used. Oxygen procured
under Federal Specification BB-0-925A is intended
for technical use and should NOT be used in air-
craft oxygen systems.
12. After the completion of repairs, always
perform an operational check of the system and
make the required tests to ensure that the oxygen
is safe for use by the pilot and crew.
ONBOARD OXYGEN
GENERATING SYSTEM
Learning Objective: Identify the system
components and operation of the onboard
oxygen generating system.
The onboard oxygen generating system
(OBOGS) is an alternative to liquid oxygen
(LOX). When compared to a LOX system, the
OBOGS has several advantages. First, its
availability y may be as high as 99 percent. There
is no requirement for depot-level maintenance.
The OBOGS has no daily service requirements,
and scheduled preventive maintenance occurs at
2,000 hours. Incorporation of the OBOGS
eliminates the need to store and transport LOX.
Additionally, it eliminates the need for LOX
support equipment. The potential for accidents
related to LOX and high-pressure gases is greatly
reduced.
SYSTEM COMPONENTS
The basic components of the OBOGS are the
concentrator, oxygen monitor, and oxygen
breathing regulator. The concentrator produces
an oxygen-rich gas by processing engine bleed air
through two sieve beds. The oxygen monitor
senses the partial pressure of the gas and, if
necessary, provides a low-pressure warning to the
pilot. The oxygen regulator is a positive pressure
regulator.
SYSTEM OPERATION
The OBOGS, shown in figure 4-16, receives
engine bleed air from the outlet of the air-
conditioning heat exchanger. The partially cooled
air passes through an air temperature sensor to
a pressure reducer assembly. The air is then routed
Figure 4-16.Onboard Oxygen Generating System
(OBOGS) schematic.
to the concentrator. The concentrator has a rotary
valve that alternates the airflow over the molecular
sieve beds. The sieve beds absorb the nitrogen and
allow the oxygen and argon to pass through. TWO
molecular sieve beds are used in the concentrator
so that while one bed is absorbing, the other is
desorbing (releasing) nitrogen. This method allows
a continuous flow of oxygen to the system. After
the concentrator, the oxygen flows to a plenum
assembly that acts as a surge tank and an
accumulator. The plenum also functions as
a heat exchanger to heat or cool the oxygen to
approximately cockpit temperature. Before the
oxygen reaches the oxygen regulator, the oxygen
performance monitor senses the partial pressure
of the gas and, if necessary, provides a signal to
the pilot whenever the pressure exceeds prescribed
limits. The oxygen then flows through the
regulator to the pilots mask.
4-25
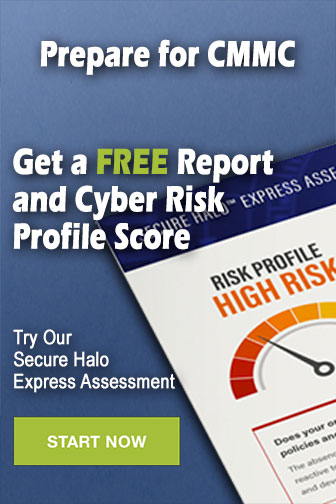