diaphragm (6) forces the demand valve lever
assembly (7) down. The pressure differential
exists during the inhalation cycle of the user by
creating a reduction in the pressure outlet (8).
4. Reduction in pressure at the pressure
outlet is sensed in the demand diaphragm chamber
(9) through the sensing port (10).
5 During periods of flow, the oxygen passes
through the venturi assembly (11). At the venturi
assembly, the flow of oxygen mixes with ambient
air, which enters the regulator through the inlet
ports (12).
6. The addition of ambient air to oxygen is
controlled by the manual diluter control lever (13)
and by the diluter aneroid assembly (14), which
automatically produces a 100-percent oxygen
concentration at altitudes above 32,000 feet.
7. The aneroid check valve assembly (15)
prevents a flow of oxygen out through the inlet
ports.
8. The emergency pressure control lever (16)
applies force to the emergency pressure control
test spring (17), which mechanically loads the
emergency pressure diaphragm (25) through the
control lever and center assembly (18). Mechanical
loading of the emergency pressure diaphragm
provides positive pressure at the regulator outlet.
9. Both automatic safety pressure and
pressure breathing at altitudes above 30,000 feet
are provided through pneumatic actuation of the
aneroid assembly (19). This function begins near
27,000 feet altitude. The force exerted on the
diaphragm assembly (20) by the aneroid assembly
actuates the pressure breather valve assembly (21),
and oxygen flows to the diaphragm and the plate
assembly (22), which is pressure loaded by this
volume of oxygen acting on the demand valve
lever assembly to the extent that the positive
pressure is built up at the pressure outlet as the
altitude increases.
10. Additional safety is obtained through the
inclusion of the second-stage relief valve assembly
(23) in the regulator.
TURNAROUND/PREFLIGHT/POST-
FLIGHT/TRANSFER INSPECTIONS. These
inspections are visual inspections performed in
conjunction with the inspection requirements for
the aircraft in which the regulators are installed.
Refer to table 4-3 for assistance in trouble-
shooting.
Visually inspect the following:
1. Electrical performance of the panel light
2. Legibility of all the markings
4-20
3.
4.
5.
6.
7.
8.
9.
Plastic lighting plate for cracks and
discoloration
Low or improper reading on regulator
pressure gauge
Emergency pressure control lever in
NORMAL position
Diluter control lever in 100% OXYGEN
position
Supply valve control lever in OFF position
Regulator and surrounding area free of dirt
and hydrocarbons
Delivery hose and connector for cuts,
fraying, kinking, hydrocarbons, and
general condition
If discrepancies are found or suspected.
maintenance control should be notified.
Regulators that do not pass inspection and
cannot be repaired in the aircraft are removed and
replaced by ready-for-issue (RFI) regulators. Non-
RFI regulators are forwarded to the nearest
maintenance activity having repair capability.
ACCEPTANCE/SPECIAL/DAILY IN-
SPECTIONS. These inspections are visual
inspections followed by a functional test. These
inspections and tests are performed in conjunc-
tion with the inspection requirements for the air-
craft in which the regulators are installed. Refer
to table 4-3 for assistance in troubleshooting.
WARNING
Make certain that when working with
oxygen, all clothing, tube fittings, and
equipment are free of oil, grease, fuel,
hydraulic fluid, or any combustible liquid.
Fire and/or explosion may result when
even slight traces of combustible material
come in contact with oxygen under
pressure.
To perform the functional test, proceed as
follows:
1. Place supply valve control lever in the ON
position.
2. Place the diluter control lever in the
NORMAL OXYGEN position.
3. Connect the oxygen hose to the quick
disconnect, place the mask to the face, and
inhale. Proper regulator operation will be
indicated by the flow indicator assembly
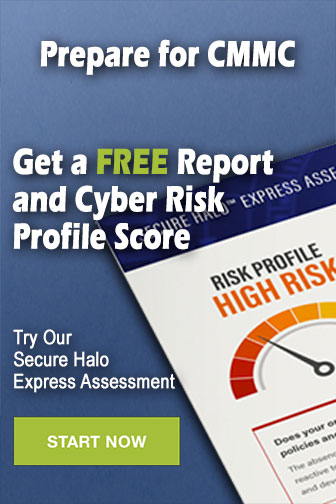