system or mechanism. For the AME,
troubleshooting is an important responsibility and
one to which he/she will devote a lot of squadron
time.
When a malfunction is reported concerning
any of the components or systems that are main-
tained by the AME, he/she must be able to locate
the trouble and correct the difficulty.
To troubleshoot intelligently, the AME must
be familiar with the system(s) at hand. He/she
must know the function of each component in the
system and have a mental picture of the location
of each component in the system in relation to
other components, as well as the location of the
component in the aircraft. This can be best
achieved by studying the installation and
schematic diagrams of the systems found in the
applicable MIM.
Troubleshooting procedures are similar in
practically all applications. The procedures
covered in this section are adaptable to almost all
aircraft systems. Auto mechanics use these steps
to find and repair automobile malfunctions. The
AME can use these procedures to find and repair
malfunctions within all the aircraft system for
which he/she is responsible.
Basically, there are seven distinct steps to
follow during troubleshooting. These steps are as
follows:
1. Conduct a visual inspection. This inspec-
tion should be thorough and searchingchecking
all lines, linkages, and components for obvious
damage, evidence of leakage, looseness, security,
material condition, and proper installation; and
servicing when applicable.
2. Conduct an operational check. The
malfunctioning system or subsystem is checked
for proper operation. This may be accomplished
by using special support equipment such as the
environmental control test set or by using aircraft
power and equipment with the engines running.
Each aircraft maintenance manual provides the
steps to be taken in performing the operational
checkout of all the aircrafts systems. The
operational checks and troubleshooting charts
for each system are numbered so that when
a malfunction occurs during a step in the
operational checkout, the malfunction can be
located under the same step number in the
troubleshooting chart. The troubleshooting chart
will provide a list of the most probable causes of
the malfunction in the order of probability, along
with a recommended remedy. In any case, the
AME must check the system out thoroughly,
3-36
observing proper operation, sequence of events,
etc.
3. Classify the trouble. Malfunctions usually
fall into three basic categorieselectrical,
mechanical, and/or improper installation. Using
the information acquired in steps 1 and 2, the
AME determines under which category the
malfunction occurs. Proper use of the test set or
a multimeter will identify whether the trouble is
electrical or mechanical. Use of the MIM when
performing all maintenance tasks should prevent
improper installation. Something affecting the
flow of gas or liquid (as could be the case in the
vapor cycle ACS) could be categorized as a
combination electrical/mechanical failure. Most
mechanical failures should be found on the visual
inspection; however, drive shaft failure on some
of the air-conditioning valves is not readily
apparent until the valve is operated. In some cases
it may even be necessary to disconnect the valve
from the ducting so that the butterfly valve can
be observed through the end opening. The
position indicator on some valves can indicate that
the valve is changing positions, which would be
a false indication if the shaft was broken after the
indicating mechanism, or if the butterfly valve was
damaged in such a manner that the shaft would
rotate without actually repositioning the valve.
4. Isolate the trouble. This step calls for sound
reasoning and a full and complete knowledge of
how each component and the system should
operate. During this step, the AME can make full
use of his knowledge and the system schematics
to trace system operation and systematically
eliminate components. He can then arrive at a
reasonable conclusion concerning the cause of the
malfunction based on facts and deductive reason-
ing. Usually the trouble can be pinned down to
one or two areas. By checking each individual area
or component, the trouble can be isolated.
5. Locate the trouble. This step is used to
eliminate unnecessary parts removal, thus saving
time, money, and man-hours. Once the AME has
isolated the trouble to a certain area or
component, a closer observation of the valve or
component in operation should provide some
obvious indication that it is not operating as
specified in the MIM. If all evidence indicates that
the problem is electrical, the assistance of an AE
should be requested.
6. Correct the trouble. This step is performed
only after the trouble has been definitely pin-
pointed and there is no doubt that the AMEs
diagnosis is correct. Removal, replacement, or
repair of the unit or system is done using the
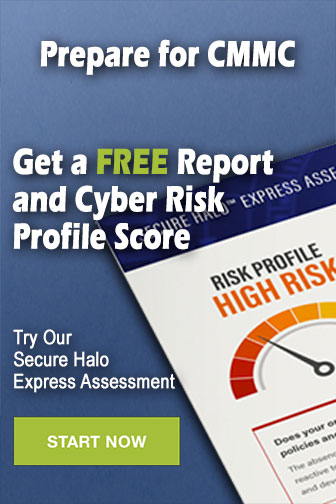