Some metals are more active than others. The
degree of attack depends upon the relative activity of
the two surfaces in contact. The more active or easily
oxidized surface becomes the anode and corrodes. In
plated metal, the possibility of dissimilar metal
corrosion becomes a factor only if there are defects in
the plating. Moisture penetrates and galvanic cells
form because of these defects.
Stress Corrosion
Stress corrosion is caused by the combined effects
of tensile stress and corrosion. Stress may be internal
or applied. Internal stresses are produced by
nonuniform deformation during cold working, by
unequal cooling from high temperatures during heat
treatment, and by internal structural rearrangement
involving volume changes. Stresses set up when a
piece is formed. Stress induced by press-and-shrink
fits and those in rivets and bolts are examples of
internal stresses. Concealed stress is more important
than design stress because it is difficult to recognize
before it exceeds the design safety factor. The
magnitude of the stress varies from point to point
4-24
Figure 4-13.Stress corrosion cracking.
within the metal. Stresses that approach the yield
strength of the metal promote stress cracking (visible
at this point), but failure can occur at lower stresses
(fig. 4-13). Most often, stress cracks are not visible to
the naked eye and are discovered in the nondestructive
inspection (NDI) process.
Fatigue Corrosion
Fatigue corrosion is a special kind of stress
corrosion. It is caused by the combined effect of
corrosion and stress applied in cycles to a component.
An example of cyclic stress is the alternating loads to
which the reciprocating rod on the piston of a
hydraulic, double-acting, actuating cylinder is
subjected. During the extension stroke, a compression
load is applied. During the retracting or pulling stroke,
a tensile or stretching load is applied. Fracture of a
metal part due to fatigue corrosion commonly occurs
at a stress far below the fatigue limit in a laboratory
environment, even though the amount of corrosion is
unbelievably small. This is why protection of parts
subject to alternating stress is particularly important in
any environment. Figure 4-14 shows an oil cooler
blower that disintegrated because of fatigue corrosion
of a blade (shown by arrow).
Fretting Corrosion
Fretting corrosion is a limited but highly damaging
type of corrosion. It is caused by a slight vibration,
friction, or slippage between two contacting surfaces
that are under stress and heavily loaded. It is usually
associated with machined parts. Examples of these
parts are the area of contact of bearing surfaces, two
mating surfaces, and bolted or riveted assemblies. At
least one of the surfaces must be metal. In fretting
corrosion, the slipping movement on the contacting
surface destroys the protective films that are present
on the metallic surface. This action removes fine
particles of the basic metal. The particles oxidize and
form abrasive materials, which further agitate within
a confined area to produce deep pits. Such pits are
usually located in an area that increases the fatigue
failure potential of the metal. Early signs of fretting
corrosion are surface discoloration and the presence of
corrosion products in lubrication. Lubrication and
securing the parts so that they are rigid are effective
measures to prevent this type of corrosion.
205.157
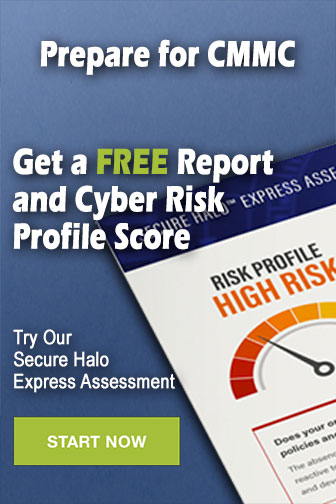