MAINTENANCE
Maintenance of the type CRU-79/P regulator
is limited to inspection, testing, adjustment of the
pressure breathing aneroid, and tightening of
loose screws. Ensure that antiseize tape is used
on pipe threads. This section contains only the
procedural steps necessary to meet these
requirements.
NOTE: Upon completion of any
maintenance action (for example, inspec-
tion, adjustment, modifications, etc.), be
sure to complete the required maintenance
data collection system forms.
If the regulator fails any inspection or testing
requirements, it must be disposed of in accordance
with any local directives and replaced with a ready
for issue (RFI) component.
The miniature regulator will remain in service
as long as it continues to function correctly and
does not require other than authorized
adjustment.
Procedural steps outlined in this section are
listed under the inspection cycle in which they are
required, and in the sequence in which they
normally occur.
DAILY/PREFLIGHT INSPECTION
The daily/preflight inspection is a visual type
inspection performed by the aircrew member to
whom the regulator is issued, either daily or before
each flight. To perform this inspection, visually
inspect the following:
WARNING
WHEN WORKING WITH OXYGEN,
MAKE CERTAIN THAT CLOTHING,
TUBING FITTINGS, AND EQUIP-
MENT ARE FREE OF OIL, GREASE,
FUEL, HYDRAULIC FLUID, OR ANY
COMBUSTIBLE MATERIALS. FIRE
OR EXPLOSION MAY RESULT WHEN
EVEN SLIGHT TRACES OF COM-
BUSTIBLE MATERIAL COME IN
CONTACT WITH OXYGEN UNDER
PRESSURE.
1. Inlet and outlet connections for security of
attachment. Make sure that all clamps, locknuts,
fittings and screws are tight.
2. The regulator body for dents, scratches,
corrosion, cracks, condition of the nameplate, or
any other damage.
3. Perform a functional test as outlined in the
next inspection (special inspections).
If discrepancies are found or suspected, the
regulator should be taken to the Aviators Equip-
ment Branch for the required corrective
maintenance.
SPECIAL INSPECTIONS
Special inspections are required at specified
intervals in addition to the daily/preflight or
calendar inspections. The interval for miniature
oxygen regulators is 30 days. This inspection
consists of a visual inspection and a functional
test, both performed by personnel of the Aviators
Equipment Branch. To perform the special
inspection, proceed as follows:
1. Visually inspect the regulator as outlined
in the previous section (daily/preflight).
2. Functionally test the regulator by attaching
the mask, regulator, and delivery tube to a suitable
oxygen supply source. Use a regulator-to-seat hose
for an attachment.
3. Turn on the supply source. There should
be a flow of oxygen through the mask.
4. Don the mask and breathe. There should
be a slight resistance on exhalation. This resistance
is due to the positive pressure feature of the
regulator.
When you finish the special inspection, record
the date and place of inspection in the NOTES
section of the Aircrew Personal Protective Equip-
ment History Card.
CALENDAR INSPECTION
The calendar inspection is performed on all
miniature regulators upon issue prior to being
installed in an in-service personal oxygen
configuration and must be performed on all
miniature regulators in service at least every 90
days.
The calendar inspection consists of a visual
inspection and a bench test. All work must be
done in a clean, dust-free and oil-free area.
VISUAL INSPECTION
To visually inspect the miniature regulator,
proceed as follows:
1. Disconnect the communication connectors.
2. Loosen the hose clamp that holds the
regulator outlet to the mask delivery hose, and
remove the regulator from the hose. Retain the
hose clamp.
12-2
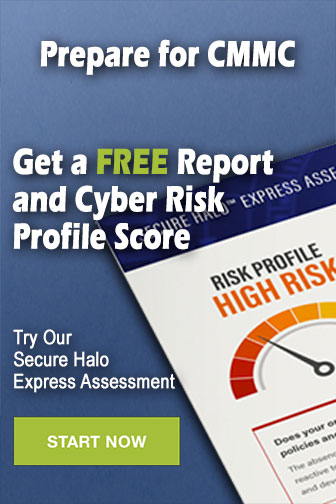