In block 18, the first two letters identify SHIPALT
(SA), ORDALT (OA), field change (FC), or any other
appropriate instruction. Electronic equipment is always
identified by serial number, and only one piece of
equipment may be reported under a given JCN. If
several pieces of the same type of equipment are altered
by field changes, there must be one document for each
piece of equipment. Example:
A ship has four C-13 Mod 1 catapults, and field change
17 is to be installed in all of them. Each catapult will be
changed, and the changes will be reported on separate
documents showing a specific JSN and equipment
serial number. This will enable the computers to
identify which items of equipment have been changed
and which have not. It also will be reflected on the
readouts returned to the ship as part of its material
history.
Another problem is the use of the noun name in
block
5.
For
electronic
equipment
the
"AN"
designation is the best entry for the noun name. If there
is no "AN" designation, the name from the nameplate
should be used. Up to 16 characters of a name may be
entered.
In block 35, a space follows each word, and words
that cannot be completed on a line are continued on the
next line with no spaces or hyphens inserted. On
deferred actions, the XXX's used to separate the trouble
from the desired corrective action must not be
separated. If they cannot be fitted in on one line, extra
spaces will be left blank on that line and the XXX's will
be put in the first spaces of the next line.
REVIEW QUESTIONS
Q7.
Maintenance Data System is used to record
what type of information?
Q8.
Under the maintenance Data System, what is
a Job Control Number?
Q9.
What is the OPNAV 4790/2K used to report?
Q10.
The OPNAV 4790/2P provide what type of
information?
SUPPLY
LEARNING OBJECTIVES: Recognize the
different types of stock and control numbers.
Recall the purpose of cognizance symbols.
Recognize sources of identifying material
when
a
stock
number
is
not
available.
Recognize the uses of the following supply
publications: FED LOG, MLC, MCRL,
MRIL, ASG, and GSA.
One of the duties of an ABE is to identify and
requisition material. This section provides basic
information to help you develop the knowledge you
need
to
perform
these
duties.
Proper
material
identification is essential to the requisitioning and
receipt of the correct item. You must understand the
terminology used in material identification.
GENERAL INFORMATION
Material
is
managed
according
to
category
(Federal Supply Classification) and its intended use.
An inventory manager is assigned for each category of
material, and has overall responsibility for all items
within the category. All items in the supply system have
an assigned two-position cognizance symbol code.
This code identifies the inventory manager and the
stores account in which the material is carried. The
items assigned to bureau, office, or systems command
for inventory management includes the following
material:
Material in the research and development stage
Material that requires continuing logistics,
engineering, or fiscal administration and control
at the department level.
Material recognized as a onetime installation
that was bought and issued for a specific use
Naval
Supply
System
Command
(NAVSUP)
Inventory Control point (ICP) items are those for which
bureau, office, or systems command management is not
essential. The NAVSUP ICP provides stocks of these
items to its segment of the supply system. This group of
items
includes
equipment,
repair
parts,
and
consumables. It also includes those items for which
stocking determination, quality control, funding, and
issue control can be accomplished by the ICP if
required, the ICP ensure that these items are available
from commercial sources and other government
agencies. NAVSUP selects the items assigned to ICP
for inventory management with the advice of the
appropriate bureau, office, or systems command.
The Navy Retail Office items are items for which
joint military supply management responsibility is
vested to the Defense Logistics Agency (DLA). These
items include components, repair parts, consumables,
and other material. The requirement determination and
procurement of these items can be accomplished by the
7-29
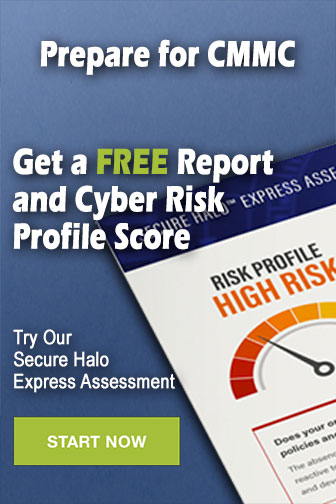