Radius. The radius (R) of the bend is always to
the inside of the metal being formed unless otherwise
stated. The minimum allowable radius for bending a
given type and thickness of material should always be
determined before you proceed with any bend
allowance calculations.
Setback The setback (SB) is the distance from
the bend tangent line to the mold point. In a
90-degree bend, SB = R + T (radius of the bend plus
thickness of the metal). The setback dimension must
be determined prior to making the bend because
setback is used in determining the location of the
beginning bend tangent line.
BEND ALLOWANCE FORMULA
By experimentation with actual bends in metals,
aircraft engineers have found that accurate bending
results could be obtained by using the following
formula for any degree of bend from 1 to 180:
(0.0173 x R + 0.0078 x T)
Where
R = the desired bend radius,
x N = B A
T = the thickness of the material, and
N = the number of degrees of bend.
Refer to the NA 01-1A-1 for the appropriate bend
allowance tables.
CUTTING SHEET METAL
Once a project has been laid out on the metal, the
next step is to cut it to shape. The type of cutting
equipment to be used depends primarily upon the type
and thickness of the material. Another consideration
is the size and number of pieces to be cut. A few
relatively thin pieces of comparatively soft metal may
be cut faster with hand-trimming methods. But for
harder metals, faster output, and more professional
results, machines designed for metal-cutting purposes
are used.
Machines used to cut sheet metal may be divided
into two groupsmanually operated and power
operated. Each cutting machine has a definite cutting
capacity that should never be exceeded. A few of the
more common types that may be available to you have
been described in the previous sections.
BENDING SHEET METAL
Straight-line bends and folds in sheet metal are
ordinarily made on the cornice brake and bar folder;
however, a considerable amount of bending is also
completed by hand-forming methods. Hand forming
may be accomplished by using stakes, blocks of
wood, angle iron, a vise, or the edge of a bench.
Bending Over Stakes
Stakes are used to back up sheet metal to form
many different curves, angles, and seams. Stakes are
available in a wide variety of shapes, some of which
are shown in figure 13-33. The stakes are held
securely in a stake holder or stake plate, which is
anchored in a workbench. The stake holder contains a
variety of holes to fit a number of different types of
shanks.
Although stakes are by no means delicate, they
must be handled with reasonable care. They should
not be used as backing when you are chiseling holes
or notches in sheet metal.
Bending in a Vise
Straight-line bends of comparatively short
sections can be made by hand with the aid of wooden
or metal bending blocks. After the part has been laid
out and cut to size, you should clamp it along the bend
line between two form blocks, which are held in a
vise. The form blocks usually have one edge rounded
to give the desired bend radius. See figure 13-34. By
tapping lightly with a rubber, plastic, or rawhide
mallet, bend the metal protruding beyond the bending
block to the desired angle.
You should gradually make the bend even. Start
tapping at one end and work back and forth along the
edge. Continue this process until the protruding metal
is bent to the desired angle. If a large amount of metal
extends beyond the bending blocks, you should
maintain enough hand pressure against the protruding
sheet to prevent the metal from bouncing. Remove
any irregularity in the flange by holding a straight
block of hardwood edgewise against the bend and
striking it with heavy blows of a hammer or mallet. If
the amount of metal protruding beyond the bending
blocks is small, make the entire bend by using the
hardwood block and a hammer.
Curved flanged parts have mold lines that are
either concave or convex. The concave flange is
formed by stretching, while the convex flange is
13-20
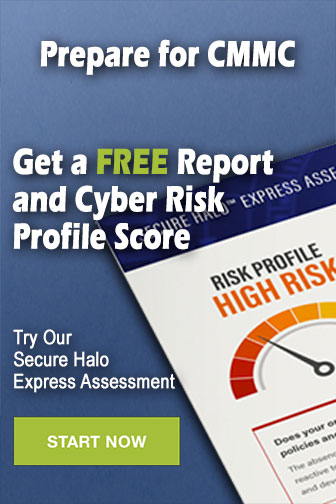