To break the arc, just release the trigger. This breaks
the welding circuit and also de-energizes the wire-feed
motor. If the wire electrode sticks to the work when it
strikes the arc, or at any time during welding, release the
trigger and clip the wire with a pair of pliers or side
cutters.
A properly established arc has a soft, sizzling sound.
The arc itself is about 1/4 inch long, or about one-half
the distance between the gun nozzle and the work. When
the arc does not sound right, you may need to adjust the
wire-feed control dial or the welding machine itself. For
example, a loud, crackling sound indicates that the arc
is too short and the wire-feed speed is too fast. Correct
this by moving the wire-feed speed dial slightly counter-
clockwise. This decreases wire-feed speed and
increases arc length. A clockwise movement of the dial
has the opposite effect. With experience, you will soon
be able to recognize the sound of the proper length of
arc to use.
The proper position of the welding torch and
material is important. The flat position of the material is
preferred for most joints because this position improves
the molten metal flow, bead contour, and gives better
gas protection.
The alignment of the welding wire in relation to the
joint is very important. The welding wire should be on
the center line of the joint if the pieces to be joined are
of equal thickness. If the pieces are unequal in thickness,
the wire may be moved toward the thicker piece.
Correct work and travel angles are necessary for
correct bead formations. The travel angle may be a push
angle or a drag angle, depending upon the position of
the gun. If the gun is angled back toward the beginning
of the weld, the travel angle is called a drag angle. If
the gun is pointed ahead toward the end of the weld, the
travel angle is called a push angle.
When the gun is ahead of the weld, it is referred to
as pulling the weld metal. If the gun is behind the weld,
it is referred to as pushing the metal. The pulling
technique is usually best for light gauge metals and the
pushing technique for heavy materials.
Generally, the penetration of beads deposited with
the pulling technique is greater than with the pushing
technique. Furthermore, since the welder can see the
weld crater easier in a pulling action, he/she can produce
high quality welds more consistently. On the other hand,
pushing permits the use of higher welding speeds and
produces less penetrating and wider welds.
WELDING SAFETY PRECAUTIONS
Accidents frequently occur in welding operations,
and in many instances, they result in serious injury to
the welder or other personnel working in the immediate
area. What many welders fail to realize is that accidents
often occur NOT because of a lack of protective
equipment, but because of carelessness, lack of
knowledge, and the misuse of available equipment.
You, the welder, should have a thorough KNOWL-
EDGE of safety precautions relating to the job. But that
is not all. You should also consider it a responsibility to
carefully OBSERVE the applicable safety precautions.
In welding, being careless can cause serious injury not
only to yourself, but to others as well.
Bear in mind that safety precautions for the
operation of welding equipment vary considerably
because of the different types of equipment involved.
Therefore, only general precautions on operating metal
arc-welding equipment are given here. For specific
instructions on the operation, maintenance, and care of
individual equipment, use the equipment manu-
facturers instruction manual as a guide.
In regard to general precautions, know your
equipment and how to operate it. Use only approved
welding equipment, and see that it is kept in good, clean
condition. Before you start to work, make sure that the
welding machine frame is grounded, that neither
terminal of the welding generator is bonded to the frame,
and that all electrical connections are securely made.
The ground connection must be attached firmly to the
work, not merely laid loosely upon it.
Keep welding cables dry and free of oil or grease
Keep cables in good condition, and, at all times, take
appropriate steps to protect them from damage. If it is
necessary to carry cables some distance from the
machines, run the cables overhead, if possible, and use
adequate supporting devices.
When you use a portable machine, take care to see
that the primary supply cable is laid separately so that it
does not become entangled with the welding supply
cable. Any portable equipment mounted on wheels
should be securely blocked to prevent accidental
movement during the welding operations.
When you stop work for any appreciable length of
time, be SURE to de-energize the equipment. When not
in use, the equipment should be completely
disconnected from the source of power.
15-36
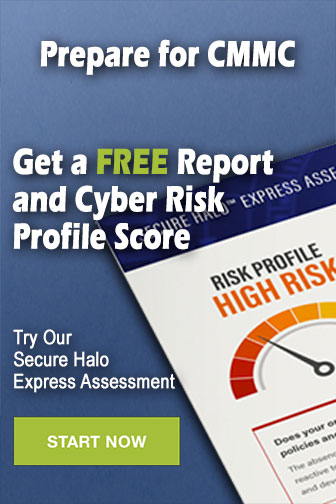