The cylinder and ram assembly constitutes the
actual engine of the arresting gear. It is located
within the engine structure between the movable
crosshead and the cylinder outlet elbow on the
engines.
The cylinder is a machined, forged steel,
smooth-bore tube, open on both ends and large
enough to provide a working area for the ram and
to house the fluid necessary for aircraft arrestments.
It is supported within the engine structure by
cylinder support saddles. One end of the cylinder is
clamped and bolted with four cylinder clamps and
Allen bolts to the cylinder outlet elbow. The other
end receives the ram. The ram end of the Mod 2
engine cylinder is stepped and counterbored on the
inside diameter to accommodate a slipper and cage
assembly, a set of V-ring packing, a retainer, and
shims. A split wiper and wiper retainer are secured
to the end of the cylinder to clean the ram as it
moves into the cylinder. The Mod 3 differs from
the Mod 2 in that the packing is installed on the
end of the ram instead of at the mouth of the
cylinder as on the Mod 2.
The ram is a large, hollow steel piston that is
moved in and out of the cylinder by the crosshead.
It is bored to reduce the weight, although it is not
bored completely through. The inner end (the end
that fits in the mouth of the cylinder) is solid and
provides a working area between the ram and
engine fluid during arrestments.
As was previously mentioned, the inner end of
the ram on the Mod 3 contains a set of V-ring
packing to provide a seal for the engine fluid
between the cylinder wall and the ram. The inner
end of the ram on the Mod 2 and Mod 3 is stepped
to accommodate a cage and slippers, which provide
a bearing surface for the ram as it slides in and out
of the cylinder.
The outer (open) end of the hollow steel ram is
clamped into a socket on the crosshead by a split
flange, which fits into an annular groove near the
end of the ram.
Crosshead and Fixed Sheave Installation
The principle involved in the operation of the
crosshead and fixed sheaves is that of a block and
tackle. The purchase cables are reeved around the
sheaves of the crosshead and fixed sheave
assemblies. The crosshead is a three-piece welded
structure with two hollow steel shafts clamped
between its outer sections and the center section.
The crosshead body is clamped to the outer end of
the ram by a split flange, which fits into an annular
groove around the end of the ram. Figure 3-14
illustrates the crosshead.
The crosshead contains two similar banks of
sheaves, with nine sheaves in each bank. The
sheaves located outboard on the crosshead are
33-inch pitch diameter, and the sheaves located on
the inboard shaft are 28-inch pitch diameter. The
difference in the pitch diameter of the two banks of
sheaves is necessary so that the purchase cable
reeved around the outboard (33-inch pitch
diameter) sheaves will clear the inboard (28-inch
pitch diameter) sheaves.
The crosshead sheaves are made of an
aluminum alloy casting and have three sections: an
inner race, a cage and roller assembly, and an outer
race. All the sheaves in the crosshead and the fixed
sheave installation rotate on roller bearings with the
exception of the 28-inch pitch diameter high-speed
sheave that fairleads the purchase cable from the
engine to the flight deck. This sheave rotates on a
ball thrust bearing. The sheaves are separated by
two-section concentric disc spacers. Each spacer has
an inner and an outer disc. The inner disc is made
of steel and provides lubrication channels from the
shaft to each cage roller assembly. The outer disc
is made of phenolic and acts as a bearing surface for
the outer sheave race; it also retains the grease.
Phenolic spacers are bonded to the sheaves on the
high-speed side only. The low-speed side has loose
phenolic spacers.
The sheaves are lubricated
through 10 zerk fittings located on the end of each
of the two hollow steel shafts (20 zerks total).
The crosshead is provided with slipper liners as
a bearing surface between the crosshead and the
crosshead tracks. There is a total of 16 slipper
liners2 on each side at the top, to prevent side
thrust, and 3 on each corner at the bottom, for a
bearing surface. Brass retainers hold the slipper
liners in place.
The fixed sheave assembly is identical in
construction to the crosshead, and all movable parts
are interchangeable. The fixed sheave assembly acts
as the stationary half of the reeve system and
therefore does not require liners. See figure 3-15.
3-18
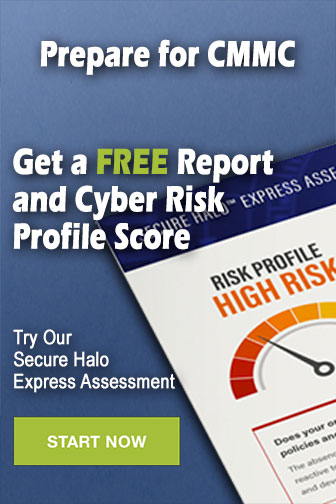