internal fluid passages for various control valve
functions. The manifold contains the bridle tensioner
pilot valve and the internal tensioning inlet and outlet
valves for the bridle tensioning system. The manifold
also contains the advance and retract pilot valve, retract
directional valve, advance directional valve, and
maneuvering valve.
The solenoid-operated bridle tensioner pilot valve
passes hydraulic fluid to actuate the bridle tensioner
control valve, internal tensioning inlet valve, and
internal tensioning outlet valve. When the solenoid is
de-energized, the fluid is allowed to flow from these
three valves to the gravity tank.
The internal tensioning inlet and outlet valves
control the flow of reduced pressure hydraulic fluid to
and from the retraction engine hydraulic motor and
orifice bypass piping. Fluid flows through the inlet
valve to the hydraulic motor and bypass piping and is
returned to the gravity tank through the outlet valve.
This enables the hydraulic motor to rotate the drum
slowly so that the static friction in the retraction engine
and drive system is overcome.
The advance and retract pilot valve controls the
advance directional valve and the retract directional
valve through the advance dump valve and the retract
dump valve, respectively. When the advance solenoid
is energized, the piston in the pilot valve is shifted, and
hydraulic fluid flows through the valve and through the
advance dump valve to shift the advance directional
valve. When the retract solenoid is energized, the piston
is shifted, and hydraulic fluid flows through it and
through the retraction dump valve to shift the retract
directional valve.
Maneuvering Valve
The maneuvering valve (fig. 4-51) is mounted on
the manifold and is operated by the maneuver forward
solenoid and the maneuver aft solenoid. This valve is
energized automatically during the latter part of the
advance and retraction operation to control the speed of
the grab after braking has been completed. Hydraulic
fluid flowing through the valve to and from the
hydraulic motor is controlled by orifices. At times other
than during normal operations, the valve can be
energized to slowly maneuver the grab, shuttle, and
pistons forward or aft for testing or maintenance. A
manual override button on the valve can be pushed to
maneuver the grab aft in case of power failure and
permit disengagement of the aircraft from the shuttle.
Two dump valves are mounted on the retraction
engine frame. The valves are operated by cams mounted
on the retraction engine frame. When the retraction
engine nears the end of the advance stroke, the advance
dump valve is actuated. The dump valve closes,
allowing the pilot-actuating fluid from the advance
valve to return to the gravity tank, initiating the
advance braking stroke. When the retraction engine
nears the end of the retraction stroke, the retraction
dump valve is actuated. The dump valve closes,
allowing the pilot-actuating fluid from the retract valve
to return to the gravity tank, initiating the retract
braking stroke.
The vent valve panel is located on top of the
retraction engine manifold assembly. Vent valves are
mounted on the panel and connect to various points in
the retraction engine hydraulic system. These valves are
used to bleed air from the hydraulic lines.
Main Hydraulic Accumulator
The main hydraulic accumulator (fig. 4-52) consists
mainly of a cylinder and a floating piston. The
accumulator maintains a constant pressure in the
hydraulic system. Hydraulic fluid on one side of the
piston is maintained in a pressurized condition by air
pressure on the other side. The piston prevents the
mixing of the fluid and air. As hydraulic fluid is used,
the air pressure causes the piston to move toward the
fluid end of the accumulator cylinder maintaining
pressure on the fluid. Fluid used from the accumulator
is replenished by the main hydraulic pumps.
Stroke-Control Actuator
The stroke-control actuator is mounted in the
bottom of the accumulator cylinder. The actuator is a
lever-operated cam that operates two limit switches. The
bottom limit switch controls the operation of hydraulic
pump No. 1, and the top limit switch controls the
operation of pumps No. 2 and No. 3. When the
accumulator piston moves toward the top of the
accumulator, the actuator causes the pumps to pump
hydraulic fluid (go onstroke) to the accumulator. Bolts
on the onstroke cam actuate the limit switches so that
pump No. 1 will go onstroke before pumps No. 2
and No. 3. When the piston nears the bottom of the
accumulator, the actuator causes the pumps to stop
pumping (go offstroke). Bolts on the offstroke cam
actuate the limit switches so that pump No. 1 will go
offstroke before pumps No. 2 and No. 3.
4-41
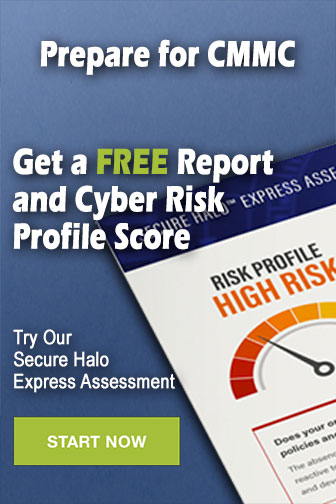