The achievement of QA depends on prevention,
knowledge, and special skills as they are described.
Prevention is the power to regulate events
rather than being regulated by them. This extends
to the safety of personnel, the maintenance of
equipment, the training of personnel, and all aspects
of the total maintenance effort.
Knowledge is derived from factual
information. Knowledge is acquired through data
collection and analysis as a means of identifying,
tracking, and preventing defects.
Special skills are those skills possessed by
the personnel trained in the technique of data
analysis and supervision of the QA program.
The QA program provides an efficient method
of gathering and maintaining information on the
quality, characteristics of repair parts, maintenance
procedures, training, and on the source and nature
of defects and their impact. The QA program
permits maintenance and operational decisions to be
made based on facts rather than intuition or
memory, by providing comparative data that is
useful long after the details of a particular event has
been forgotten.
A properly functioning QA program points out
problem areas to maintenance managers so that
appropriate action can be taken to accomplish the
following:
Improve the quality, uniformity, and
reliability of the total maintenance effort
Improve the work environment and the tools
and equipment used in the performance of
maintenance
Eliminate unnecessary man-hour and dollar
expenses
Improve the training, work habits, and
procedures of maintenance personnel
Increase the accuracy and value of reports
and correspondence originated by the division
Distribute required technical information
more effectively
Establish realistic material and equipment
requirements in support of the maintenance effort
Support safety and FOD prevention and
reporting programs
QUALITY ASSURANCE BRANCH
ORGANIZATION
The QA branch is comprised of a small group of
skilled personnel who are permanently assigned to
the branch. They are responsible for conducting
Q A I - l e v e l
i n s p e c t i o n s
a n d
t h e
management/monitoring of QA programs in the
division. Additionally, personnel assigned to other
branches and work centers will be designated to
perform certain inspection functions NOT requiring
QAI-level involvement. These personnel are CDIs,
who are assigned to inspect specific steps of a
maintenance procedure performed by their
respective work center. They are responsible to the
QA branch supervisor while performing QA
functions. CDIs are NOT permitted to inspect their
own work under any circumstance.
It may also be necessary to augment the QA
branch with CDQAIs to temporarily alleviate given
skill or manpower shortages. (When augmentation
for a period of more than 90 days is required, a
letter containing information surrounding the
shortfall and justification of the request for
continued augmentation must be submitted to the
cognizant type commander for approval.)
RESPONSIBILITY FOR QUALITY OF
MAINTENANCE
To establish a successful QA program, everyone
in the maintenance organization must fully support
it. It is not the training, maintenance instructions,
or other facilities that determine the success or
failure of a QA program, it is the frame of mind of
all assigned personnel.
Each person must know that quality work is vital
to the effective operation of the maintenance
organization. Each must know the specifications
required to achieve quality work, as well as the
purpose of those specifications.
The person most directly concerned with and
responsible for quality workmanship is the work
center supervisor. This stems from his responsibility
for the proper professional performance of assigned
6-14
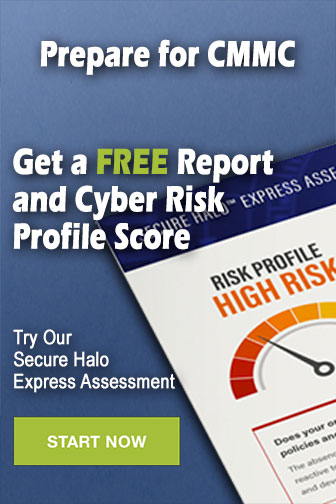