Section I is the INFORMATION section. This
section contains job identification information;
including the job control number, consisting of the
Julian date, work center identification code, and the
job sequence number.
It also identifies by noun
name and equipment identification code the system
and equipment that maintenance is to be performed
on. When discovered, the action taken, cause, and
malfunction codes are also recorded in this section.
(A complete listing of applicable codes is found in
Appendix D of OPNAVINST 4790.15.)
The
equipment serial number and meter reading, if
applicable, type of maintenance requirement, and
equipment compartment location completes the job
information section.
Section II is the COMPLETED ACTION
section. It contains the signatures of the person
who actually performed the maintenance, the
QAI/CDQAI or CDI who inspected the
maintenance, the branch supervisor who verified
that all maintenance and inspections have been
completed, and approval of the ALRE maintenance
officer or the maintenance control chief to return
the equipment to operational status. The JOB
COMPLETION DATE and type commander
(TYCOM) availability screening blocks are also in
this section.
Section III is used for MANPOWER
ACCOUNTING. The job start and stop dates, start
and stop times, the number of people assigned to
the job, and the total man-hours expended are
recorded here.
Sections
IV,
V,
and
VI
contain
MAINTENANCE INFORMATION.
This
information includes, but is not limited to, a
description of the corrective action taken; the job
description, which is a summary of the problem; and
any readings or measurements that may have been
taken during the performance of the maintenance or
inspection.
Section VII contains SUPPLY DATA
INFORMATION for parts or material used during
the performance of maintenance This includes the
noun name of the part or material, the part number,
the national stock number (NSN), the quantity of
parts or material required to perform the
maintenance, the date that the parts were ordered,
the requisition number of the order, and the actual
date that the parts or materials were received by
V-2 division.
Section VIII is used to document the use of
TOOL CONTROL procedures.
Since the MAF is the major divisional record of
all maintenance performed, it is necessary to make
sure that proper administrative procedures are
followed to establish historical data concerning all
ALREs. Therefore MAFs and all maintenance
information will be retained as follows:
Corrective maintenance action MAFs will be
retained for a period of 1 year. Copy 2 of the MAF
will be retained by the maintenance responsible
work center. Copy 1 will be retained by the QA
branch.
Preventive maintenance action MAFs must
be retained for the most recent PMS action
performed only.
Monthly, an automatic data processing
(ADP) MAF update is Performed. This is a
transfer of MAF information to floppy disks
submission to the Naval Air Warfare Center,
statistical and historical data collection.
A copy of all data disks will be retained
one complex overhaul (COH) period.
PMS MAINTENANCE REQUIREMENT
STATUS BOARDS
for
for
for
Maintenance requirement (MR) status boards
are tools used to track critical scheduled/situational
maintenance and inspections required on catapults
and arresting gear equipment. These requirements
are based on calendar periods (daily, weekly,
monthly, and so on) and the total number of
catapult shots or arresting gear arrestments (hits)
accumulated. Documentation of shots and hits is
therefore mandatory to ensure that prescribed
maintenance and inspection requirements are
performed on time.
Maintenance requirement status boards (figs. 6-6
and 6-7) are locally produced or procured. As a
minimum these boards will contain information on
each shot- or hit-related maintenance task specified
in the PMS system.
The minimum information
elements required are the following:
Maintenance requirement periodicity code
(M-1, Q-1R, 24M-2R, and so forth)
6-10
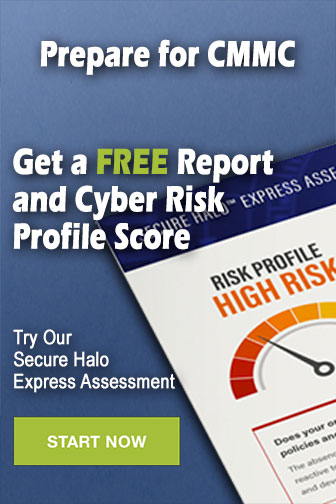