Planning and submitting budget requests for
the funding of tools, spare parts, and materials
necessary for the proper operation and maintenance
of ALRE
Maintaining OPTAR expenditure logs and
records
Requisitioning parts and materials to
support ALRE operations and maintenance
Establishing and maintaining an effective
tool control program
All personnel in the maintenance organization
are subordinate and responsible to the maintenance
officer. As work center group supervisors and work
center supervisors, they are responsible for the
maintenance of all systems and equipment assigned
to their work centers. Both the group and the work
center supervisors
direct and manage the
maintenance program in their work centers,
supervise the day-to-day ALRE operations, ensure
proper documentation of preventive and corrective
maintenance,
and
maintain
effective
communications between the work centers and MC
to ensure an up-to-date maintenance profile of the
division.
They also direct assigned work center
personnel in the performance of their duties and the
daily operation of ALRE equipment. Group and
work center supervisors are also responsible for the
following:
Keeping MC informed of all problems and
equipment status in the work center.
Updating and validating information on the
Visual Information Display System (VIDS) board
with MC daily.
Ensuring
that
all
maintenance
documentation is complete and correct.
Being knowledgeable of procedures for
ordering spare parts, from initial need identification
through material receipt.
Being knowledgeable of operating space
item (OS1) operations and listings. (Stocking of
OS1s is a Supply Department function, but inputs
for stocking originate with the work center.)
Maintaining strict tool control accountability
within the work center.
Recommending qualified and responsible
personnel to be CDIS for the work center.
Ensuring that QAIs/CDQAIs or CDIS are
available for all tasks requiring QA inspection.
Assisting the QA Branch in implementing
and maintaining support for the division safety
program by conducting safety training in the work
center, using and promoting practices to enhance
safety, and reporting all accidents and unsafe
practices, procedures, or conditions.
Assisting work center branch officers in
maintaining the training program by ensuring
optimum use of personnel through job assignments
based on prior training and experience, that formal
in-service training is conducted, that on-the-job
training (OJT) is conducted under the supervision of
qualified work center personnel, and that Personnel
Qualification Standards are administered according
to established procedures.
Maintaining required reading files and
ensuring that all assigned work center personnel
read and initial the information contained in them
on a monthly basis.
Ensuring that all work center required
publications are available and maintained with
current changes.
VISUAL INFORMATION DISPLAY
SYSTEM (VIDS)
The division maintenance profile is a visual
display of current maintenance information
maintained by the maintenance control chief
through the use of the VIDS and the maintenance
requirement (MR) status boards.
These are
important management tools in the maintenance
program because they provide a graphic display of
vital up-to-date information.
The VIDS board displays all maintenance status
information-particularly system problems or failures
and supply statusproviding the ability to review the
overall maintenance situation quickly. This allows
the maintenance officer, maintenance control chief,
6-5
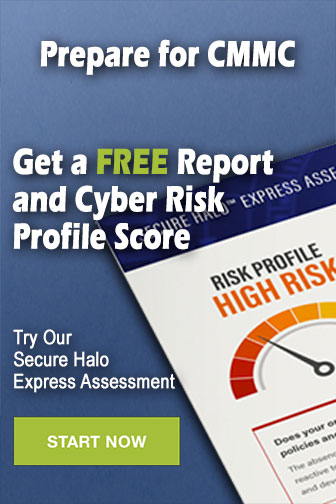